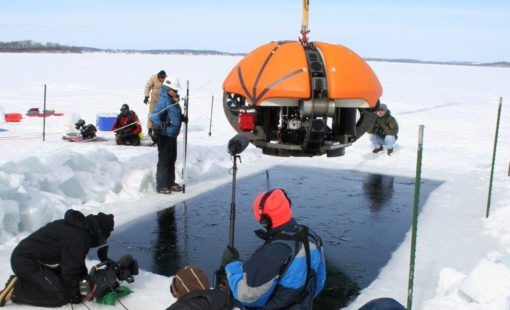
- Case Study
Stone Aerospace faced the pressure of a tight schedule in designing a one-of-a-kind underwater autonomous vehicle (AUV). The time needed to design the wiring harness for the AUV was reduced by around 12 weeks and $20,000 was saved by using E3.series to automate many aspects of the design process, while integrating the logical and physical design on a single platform.