1:1 scaled panel drawings
E3.panel - Electrical Panel and Switch Cabinet Design
Our electrical panel design software E3.panel allows engineers to layout components inside electrical panel enclosures in both 3D and 2D. Intelligent automatic snapping points allow parts to be easily placed in their correct location. Clashes can be prevented with keep-out and height restrictions. E3.panel is dynamically integrated with E3.schematic and E3.cable. Users can easily navigate between the panel and schematic, and changes to either are immediately reflected.
Slot and mount functionality
Keep out areas and restricted areas
Automatic wire routing in 2D and 3D
Control Panel Design and Automatic Electrical Wiring
The E3.panel design software allows engineers to layout components inside panel and switch cabinet enclosures. Intelligent automatic snapping points allow parts to be easily placed in their correct location, and with keep-out and height restrictions it is also possible to prevent clashes.
Signal logic is transferred from the schematic and wires can be automatically routed through ducts in the panel, taking into account the shortest route and any segregation requirements, duct fill capacity is also checked. The length of each wire is calculated and with dedicated links to wire preparation machines wires can be cut stripped, crimped, and marked automatically.
E3.Panel Key Features
The software for electrical panel design is dynamically integrated with E3.schematic and E3.cable. The design can begin either in the panel or the schematic. Users can easily navigate between the panel and schematic and changes to either are immediately reflected across both.
Working in either two or three dimensions, E3.panel allows engineers to layout components inside switch cabinets and electrical panel enclosures. Intelligent automatic snapping points allow parts to be easily placed in their correct location, and with keep-out and height restrictions it is also possible to prevent clashes.
Intelligent automatic snapping points allow parts to be easily placed in their correct location, and with keep-out and height restrictions it is also possible to prevent clashes. Wires can be automatically routed through ducts in the electrical panel, taking into account the shortest route and any segregation requirements. Duct fill capacity is also checked.
E3.panel automatically calculates the length of each segment. If E3.panel’s links to wire preparation machines are used, wires can be cut, stripped, crimped, and marked automatically.
Using VRML or STEP AP203/214 all 3D data in E3.panel can be transferred to 3D mechanical systems. Simplified models of the electrical design are used to check for collisions in the complete mechanical design. This functionality enables full digital mock-ups to assess spacing requirements, clash detection, and error prevention.
Manufacturing data can be extracted from the electrical panel design in the form of wire lists, which include route and length information. In addition, various modules are available, which interface
E3.panel to manufacturing equipment such as Komax wire preparation machinery and Perforex drilling, punching, and cutting tools.
E3.panel is part of the Smart Cabinet Initiative.
Related products
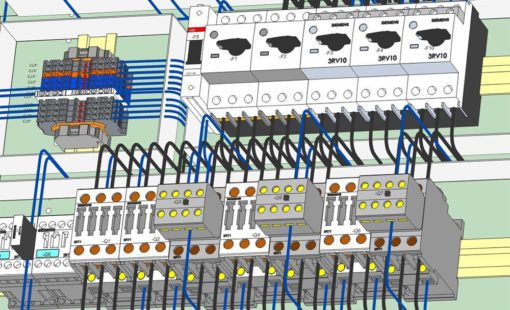
- Products
E3.panel+ enables automatic wire routing within the panel enclosure. Connectivity data from the schematic is automatically available in the panel design, and a shortest route algorithm routes the wires through cable ducts.
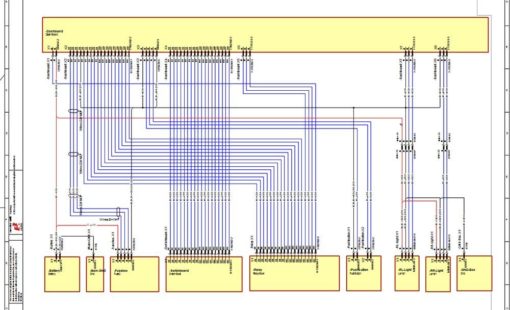
- Products
E3.cable extends the functionality of E3.schematic enabling individual conductors to be combined together in the design to form cables and harnesses.
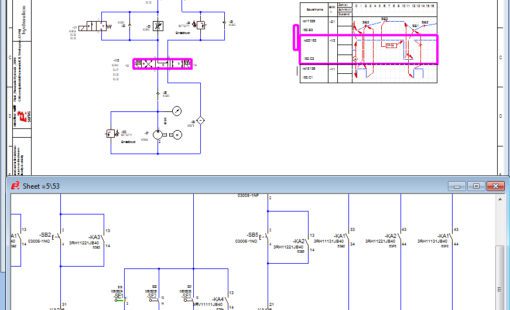
- Products
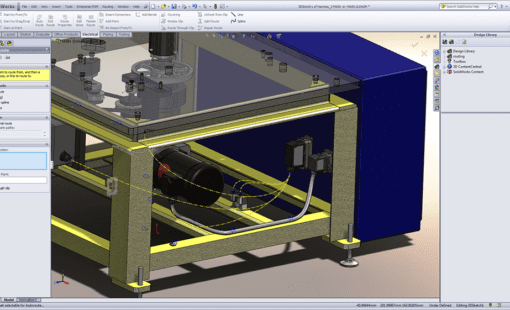
- Products
E3.3DRouting Bridge - Streamline ECAD-MCAD collaboration by synchronizing connectivity data between E3.series and leading MCAD platforms in real-time.
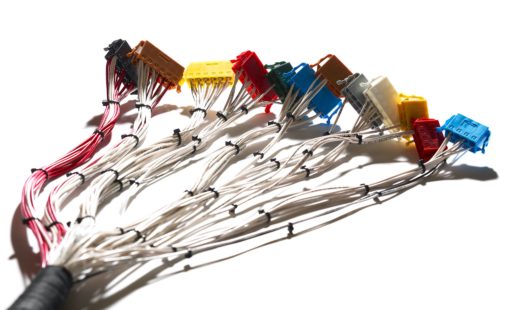
- Products
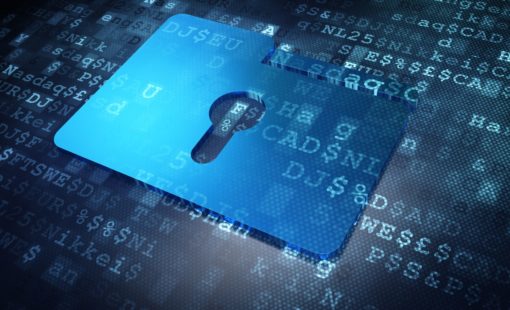
- Products
Related Resources
Find out more via our webinars, press releases and more...
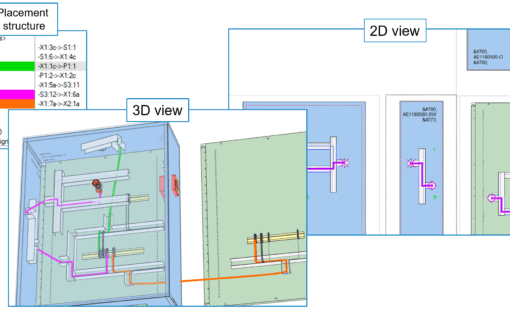
- Webinar
In this Smart Cabinet Building webinar, we will present you a selection of new functions of the E3.series 2022 release. This session concerns enhancements in E3.panel, as well as the tools for manufacturing automation, in particular E3.CutOut, E3.ExportToKomax and E3.WiringCockpit.
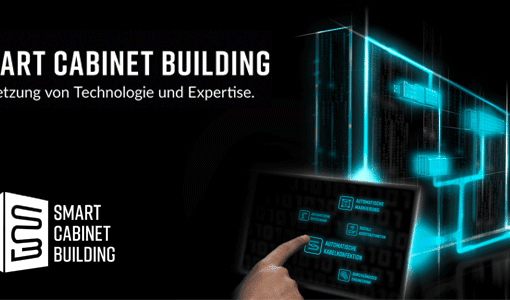
- Webinar
This webinar will show you how digital product data can support you to develop and produce your control cabinet faster and in a more flexible and economical way.
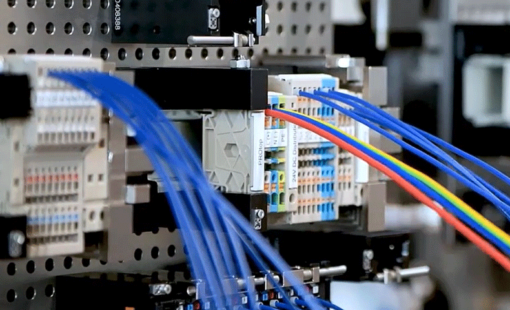
- Webinar
This webinar will provide details and demonstrations of the various tools available to help support the manufacturing automation of cabinet / panel designs.

- Webinar
Get an overview of the Smart Cabinet Building initiative - a best-in-class turn-key solution for the design, manufacture and assembly of control cabinets by bringing together industry leading expertise from Weidmueller, Komax, Zuken and Armbruster Engineering.
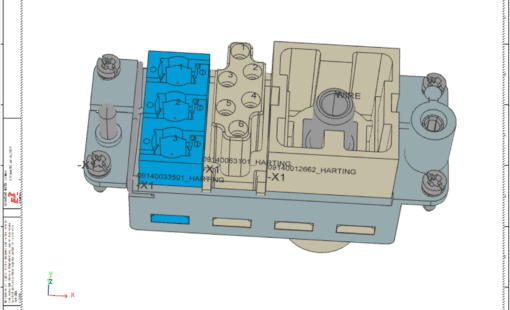
- Press Release
E3.series 2021 from Zuken delivers enhancements for connector handling, 3D control cabinet design and ECAD/MCAD collaboration.
Recent E3.panel Blog Posts
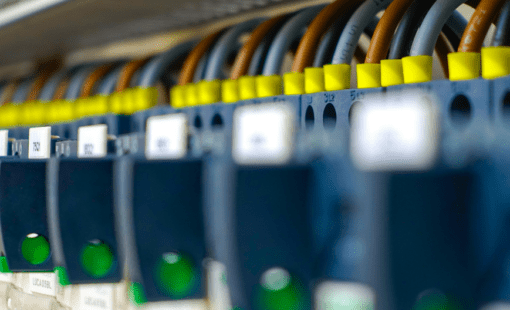
- Blog
For decades 3D has been the state of the art in the world of mechanical design. In electronics and electrical engineering, 2D still holds its own, because here the logical schematic forms the basis for the entire design. The third dimension doesn't come into play until physical design - but 3D is becoming increasingly important there. Find out why on our blog.
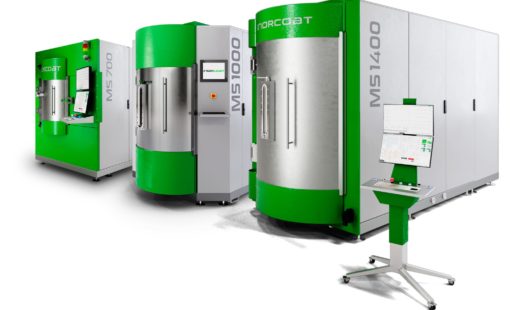
- Blog
INORCOAT relies on E3.series for the development of environmentally friendly nanotechnology coating systems. The first system was recently put into operation at the Portuguese National Bank for the coating of dies for euro coins.
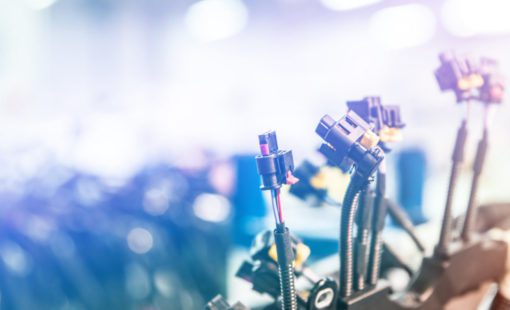
- Blog
An immature design or manufacturing process leads to excess complexity. Smart manufacturing options driven by intelligent design solutions provide a repeatable and efficient path to simplify manufacturing processes.
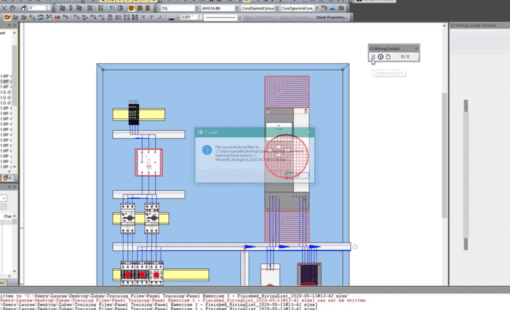
- Blog
E3.WiringCockpit is a great Cabinet Production tool to use alongside with E3.series. Making it easier to connect between engineering and manufacturing...
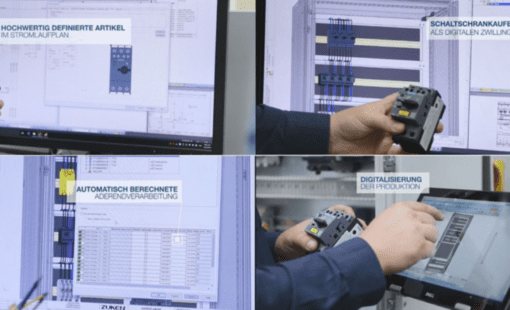
- Blog
Reducing costs, increasing productivity and ensuring quality – this is the wisdom that every management consultant in the manufacturing industry has in their briefcase today. In fact, over the past two decades, the industry has allocated significant budgets to achieve these goals. At the same time, companies often overlook money that is literally lying on the shop floor in the form of obsolete paper-based transitions to manufacturing – in particular in the areas of electrical engineering and assembly.
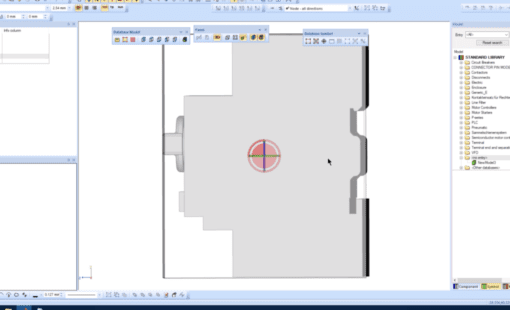
- Blog
This video will show step by step instructions on how to create a basic Panel Model and insert a 3D STEP file.