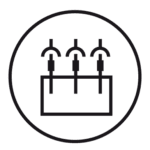
Ideally suited for engineers and designers working with DC control systems
E3.eCheck is an extension to E3.series that enables users to analyze their electrical schematic circuits with functional circuit tests and check designs for fuse and wire sizing errors. The utility works in real-time and provides instant feedback on the operability of the circuit design.
Ideally suited for engineers and designers working with DC control systems
For automotive, aerospace, railway, and special purpose vehicle applications
Works in real-time and provides instant feedback on the operability of the circuit design
In order to facilitate the functional circuit tests, special objects exist in the E3.series library, including power sources, fuses, switches, complex devices, and loads. Power supplies allow the user to simulate the circuit while fuses monitor the inline current.
Switches can be activated allowing current to pass between their contacts, and complex devices such as relays are configured to open or close auxiliary contacts based on the coil operation.
During the analysis and design phase, the current value and direction are constantly monitored at pin level. The voltage drop is monitored at each pin to determine the effectivity of the circuit.
Inline fuses will fail should their tolerance be exceeded. This allows users to correct designs during the prototype or development phase – long before products enter the manufacturing stage.
Switches and contacts within the design are controlled by the voltage and current passing through the circuit. Energizing a coil will open and close auxiliary contacts, which in turn enables or disables current flow in other sections of the design simulating the real-life operation of the circuit. As current passes through to the load, objects such as lamps or motors voltage are checked and success or failure information is fed back to the user.
E3.eCheck complements the comprehensive capabilities of E3.series. With its electrically-aware component library, specifically-designed kernel and numerous design rule checks, it is optimized for electrical design. Connector mates, connector pin terminals and cavity seals are automatically assigned and short-circuits and incorrect part usage is prevented, ensuring that correct design data is always available for manufacturing.
Satisfied customers
Related Resources
Find out more about DC Functional Analysis and Circuit Checks via our webinars, blogs, press releases and more...
Design errors due to tolerance violations often lead to the expensive recall of vehicles and equipment. Detection and correction of these errors early in the design chain can eliminate downstream headaches.
Mecalac designs and manufactures heavy plant vehicles for use in construction. Their vehicles – backhoe loaders, site dumpers and compaction rollers – are each offered in several variants. They all need to work in harsh environments.