Knowledge-based determination of weight and cost enabled by models developed by Zuken using AI-methodologies
E3.WiringSystemLab
E3.WiringSystemLab enables the optimization of wiring harnesses with an unprecedented degree of speed and accuracy. With these capabilities, it generates substantial benefits across a wide spectrum of applications in the automotive and transportation industry.
Representation of different variants and configurations within one single project enables evaluation of different implementation approaches
A powerful analysis and compare functionality helps engineers determine the most suitable solution in a minimum of time
Support of standard formats such as KBL, VEC, PLMXML or Excel® ensures easy integration into CATIA® or Siemens NX® environments
Wiring harness design and optimization for min. weight and cost
Wiring harness analysis and optimization of their designs to meet targeted weight and cost objectives is a complex and challenging task. One of the most time-consuming aspects is the consolidation of different data sources and inputs into one consistent representation. Topology data, in particular, have been known to require an intense effort for consolidation, as different segments have to be combined to one single representation and then routed manually in a 3D environment (e.g. CATIA® or Siemens NX®).
E3.WiringSystemLab simplifies this complex task with direct 3D data modeling capabilities and automated wire harness assembly functionality supporting the compilation of comprehensive wiring loom designs from heterogeneous fragments. The result is a substantial reduction of ramp-up and optimization cycles.
E3.WiringSystemLab enables the optimization of wiring looms with an unprecedented degree of speed and accuracy. With these capabilities it generates substantial benefits across a wide spectrum of applications in the automotive and transportation industry.
E3.WiringSystemLab integrates seamlessly into existing E3.series environments, reading in schematics data directly from the E3.cable data model. In addition, standard interfaces such as KBL, VEC, PLMXML as well as generic Excel files are supported.
With these capabilities, E3.WiringsSystemLab also lends itself for system optimization tasks that are embedded into third-party environments.
E3.WiringSystemLab is committed to supporting all relevant industry-standard formats. With its support of the VEC format, E3.WiringSystemLab leads the industry by anticipating the next generation industry standard for wire harness designs.
For the customer, this means substantial benefits in terms of easy integration into existing environments as well as the protection of investments in legacy data. Our Software for wiring looms seamlessly integrates into E3.cable.
Information between the toolsets is provided by a process-to-process coupling. No file transfer is required to read in schematic information into E3.WiringSystemLab.
A highlighting functionality enables cross probing between E3.WiringSystemLab and E3.cable. This cross-reference is also maintained through the technology repartitioning process and ultimately becomes available in E3.HarnessAnalyzer in combination with the related 3D structure.
Topology structures can be accessed and manipulated directly in a 3D environment. Particular attention was dedicated to an intuitive user interface enabling casual users to access and modify 3D structures without requiring specific training. Powerful, yet easy-to-use functionality is also available to support typical topology modification tasks, such as inserting connectors, packaging components by drag & drop or 3D mirroring.
To compare different implementation approaches, E3.WiringSystemLab provides powerful concept evaluation capabilities. An online-indicator is available directly in the user interface, with which trends for key values can be indicated. Details can be access with just one additional click. In addition a dedicated comparison tool is available that visualizes differences between versions on a detailed level down to single wires or connectors.
Related Items
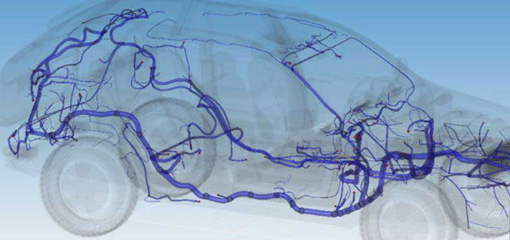
- Webinar
This webinar will cover optimizing wire harness designs to meet targeted weight and cost objectives which is a complex and challenging task. One of the most time-consuming aspects is the consolidation of different data sources into one consistent representation.
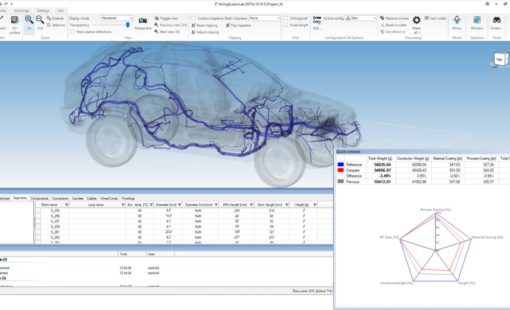
- Press Release
- Datasheet
Related E3.series products
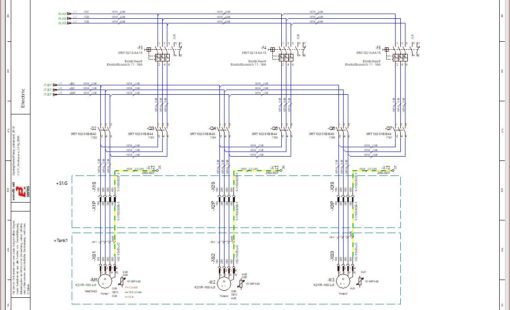
- Products
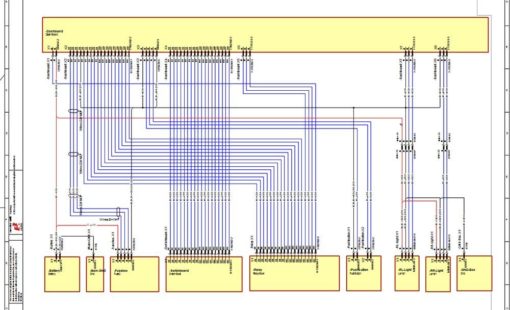
- Products
E3.cable extends the functionality of E3.schematic enabling individual conductors to be combined together in the design to form cables and harnesses.
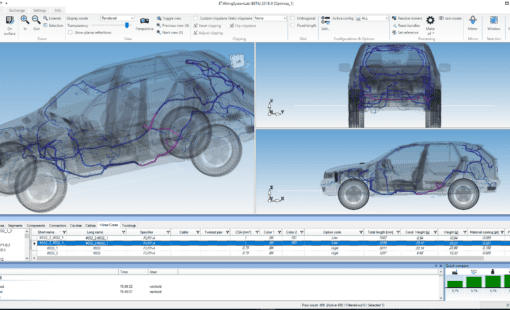
- Products
Sharing comprehensive harness design models and documents with internal or external project teams.