Seit mehr als 10 Jahren sind die Entwicklungswerkzeuge an allen Kompetenzzentren
standardisiert. Damit wurden die Voraussetzungen geschaffen für die Realisierung
wichtiger Synergieeffekte in Sachen Standardisierung elektronischer Bauteile,
Wiederwendendung von Designs und modularer Entwicklung
Der Industrie-Messtechnik-Spezialist Endress+Hauser hat die PCB-Entwicklungs- und Freigabeprozesse über alle Entwicklungsstandorte hinweg mit Daten- und Prozessmanagement-Lösungen von Zuken standardisiert und so die Grundlagen für eine unternehmensweite Standardisierung von Entwicklungsprozessen und –methoden geschaffen.
Auf einen Blick
Die Überlegungen gingen von Anfang an über die reine CAD-Software hinaus in Richtung Synergie-Effekte für Standorte und Kompetenzzentren: „Wir waren uns im Klaren, dass eine einheitliche CAD-Software alleine nur sehr eingeschränkte Möglich keiten zur Nutzung von Synergieeffekten bot. Da jedes Product Center mit einer eigenen und jeweils unterschiedlich aufgebauten Bauteildatenbank arbeitete, war eine Wiederverwendung vorhandener Design in neuen Projekten nicht möglich“, sagt Paul Burger, Group Leader PCB R&D.
Alle an den verschiedenen Standorten verwendeten Komponenten über ein einheitliches Materialnummernsystem verwaltet. Unter jeder Materialnummer sind dabei auch freigegebene und zugelassene Second-Source Komponenten hinterlegt, so dass für eine sichere Produktionsplanung die erforderlichen Komponenten zuverlässig beschafft werden können.
Heute werden alle Design-Daten der Endress+Hauser Gruppe in DS-2 von Zuken verwaltet und bereitgestellt. Jeder Berechtigte im Unternehmen kann auf die für seine Aufgabe erforderlichen Daten in Rahmen seines Berechtigungsprofils zugreifen. Werden Veränderungen am Datensatz vorgenommen, erstellt das System automatisch eine neue Revision, so dass sichergestellt ist, dass zur Fertigung freigegebene Baugruppen nicht versehentlich manipuliert werden.
Related products
Discover more about the products that helped Endress+Hauser
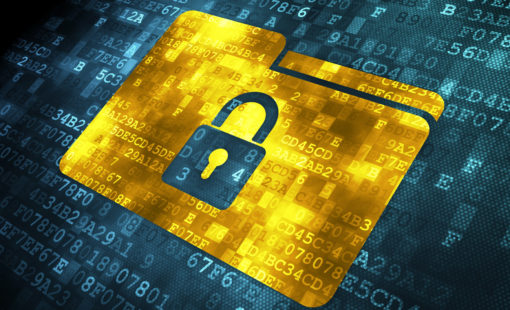
- Products
PCB Designdaten-Management. Standortübergreifende Verwaltung von Bibliotheken, Designdaten und Konfigurationen in einer einheitlichen Umgebung
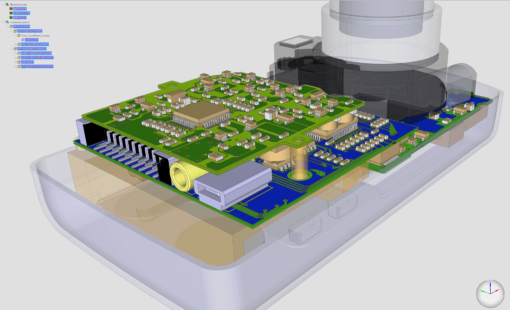
- Products
Design Force kombiniert konventionelles 2D-Design mit nativem 3D-Design und den neuesten Technologien in Benutzeroberfläche und Grafik für schnellstes Rendern und Aktualisieren.
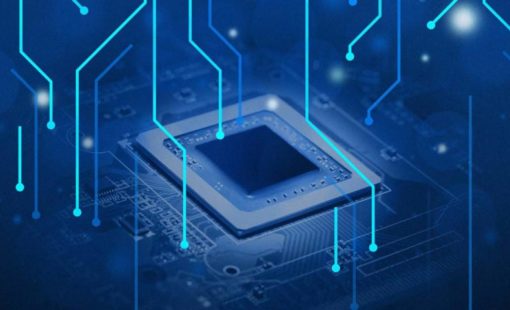
- Products
CR-8000 umfasst eine Suite von Anwendungen, die den gesamten Lebenszyklus des PCB Engineerings abdecken.