This is an exciting time in the product development world. Increasing product complexity is driving the need for a design process evolution. Not long ago the detailed design process was the centerpiece of product development. But the need for functional and physical design accuracy is forcing the product development process to evolve. In response, the product development process is both converging and expanding.
At one end, detailed design disciplines are converging. As PCB made the leap from 2D to 3D, the door opened for more cross-domain detailed design collaboration. ECAD and MCAD tools can now move models between detailed design domains. Electrical design tools for harness and panel joined the evolution with 3D support. Electrical, electronic and mechanical detailed design tools are converging with cross-domain collaboration. For example, a wire harness can now be designed in the electrical tool, moved to the 3D mechanical tool for routing and then back to the electrical tool for harness manufacturing. This detailed design convergence is adding the needed accuracy in terms of wire length. This convergence is the result of the growing need for functional and physical design accuracy due to product complexity.
But what about the design process expansion? Product complexity is driving the need for better product requirement and hardware architecture definition in the form of Model Based Systems Engineering (MBSE). MBSE is becoming the new starting point for product development. For example, a requirement for a braking system is a stopping distance of 300 feet at 60 mph. MBSE provides the product model but it needs to be realized in the form of enclosures, wires, PCBs, screws, etc. Realizing the MBSE design begins with architecture optimization – another new design phase. When entering detailed design, a poor architecture will result in a poor product.
If you are wondering what architecture optimization is, imagine you are building a new car and you have 100 electronic control units (ECUs) to place. Detailed design is great for building the ECU and the harnesses that connect them. But where do you place the ECUs in the car to minimize wire harness weight and cost? Exploring different placements and comparing cost and weight is the architecture phase. Each ECU also requires the architecture to be optimized prior to detailed design. A critical ECU architectural check would be to make sure the required functionality can fit on one board. Going to detailed design without routable boards would be a costly error. Numerous architecture questions need to be answered before proceeding to detailed design.
The product development process is evolving to include MBSE and architecture optimization as well as detailed design. Bridging these different design phases without data re-entry is the golden ring. Zuken has architecture optimization tools that bridge to detailed design, and MBSE is the next step.
Related Content

- Blog
Die Komplexität von Produkten nimmt in einem rasanten Tempo zu. Das Der Siegeszug von Elektronik, Miniaturisierung und Digitalisierung trägt dazu bei, dass machen Geräten immer intelligenter und kleiner werden. Um mit diesen Veränderungen Schritt zu halten, müssen die Hersteller die Art und Weise verändern, wie sie komplexe Systeme entwickeln.
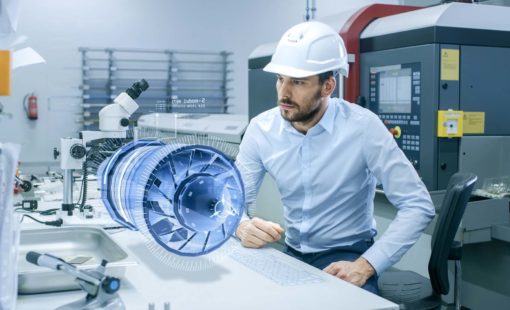
- Products
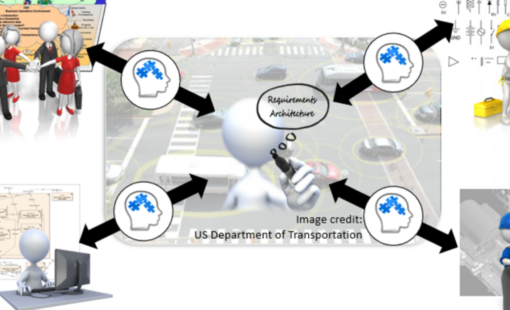
- Blog
Die Komplexität moderner Projekte wächst schneller als unsere Fähigkeit, sie zu bewältigen. Traditionelle Methoden des Projektmanagements geraten dabei zusehends unter Druck, doch Fortschritte im Bereich des modellbasierten Systems Engineering (MBSE) versprechen Hilfe. David Long, Präsident des System-Engineering-Unternehmens Vitech, erklärt, das Prinzip.