A customer recently asked me if CR-8000 Design Force could support stretchable flex designs. At first, I found the question odd, until they shared their intent: wearable electronics. The idea of wearable electronic products like head and wrist bands sparked an interesting conversation and piqued my interest.
I gave myself an action item to do a little research on the design requirements and the manufacturability of the concept. Apparently, we are approaching a decade since the first experiments with stretchable materials began at M.I.T., The University of Michigan and other esteemed institutions. We’ve come a long way in the last decade.
Currently there are PCB manufacturers supporting “stretch-rigid” and “stretch-flex” technologies. While at the PCB West 2018 conference in Santa Clara, CA, I had the chance to visit with one. Greg Vouga, who is the director of sales at Würth Electronics was kind enough to share some information with me and provide some samples of finished circuits.
You may wonder how these technologies might be used. You may initially think about wearable electronics like watches and fitness trackers. But mainly, this technology is targeted at medical applications. Some time ago I participated in a sleep apnea study and it involved being wired up with electrical sensors around my head and face. With the newest stretch-flex technology the 30-minute prep time to connect all the various sensors and wires could be eliminated by using a fitted cap that the patient can easily slip on and off. At the same time, the wearable technology makes it easier for the patient to be mobile during the study. That’s only one example, and the possibilities are growing.
The design process for stretchable circuitry requires similar design considerations for manufacture (DFM) checks as with typical rigid-flex designs such as arcs, curved traces, reinforced pads, etc. The manufacturing difference is in the materials where a polyurethane or silicone film is used to encase the stretchable/retractable wire patterns and components as opposed to polyimide Kapton non-stretchable materials. The stretch in the finished circuit is obtained by routing the copper traces using repetitive horseshoe-shaped meanders, as shown in the image below.
The mechanical limitation of the percentage of stretch over {x} amount of cycles or stretches is still a mystery that engineers will solve over time. For example, 10% stretch could be achieved over 100,000 cycles or 70% of stretch may occur over 100 cycles, just like a rubber band.
Copper weights of 0.5 oz and wire widths of 0.1mm are typical though the wires in the image above were smaller. Some cases resulted in a completed circuit only 0.015mm. The spacing in between the wires in the stretch region is sealed to prevent contact during manipulation of the article.
Getting back to the original question, “Can CR-8000 Design Force support stretchable flex designs?” The answer is of course, yes. However, the layout of the design is only part of the challenge; defining the DFM rules and checks is the other part. Zuken’s DFM/ADM (advanced design for manufacturing) rules makes it possible to check for the basics of rigid and flex design ensuring design accuracy throughout the process. As these new technologies continue to evolve with even more applications, DFM rules and checks will also evolve to support them.
Related Content
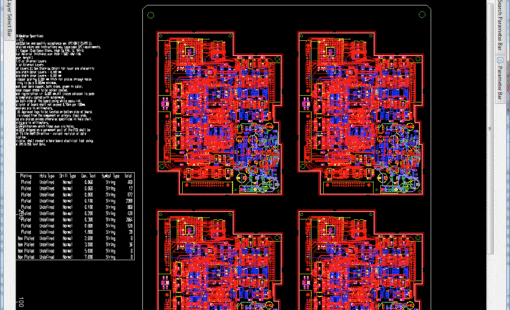
- Products
With a robust set of features for data preparation and embedded verification to verify manufacturing specifications, DFM Center addresses the challenges of the manufacturing process.
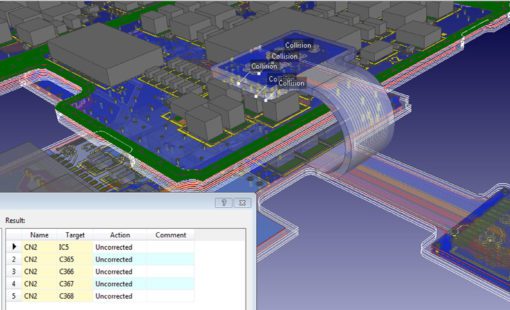
- Webinar
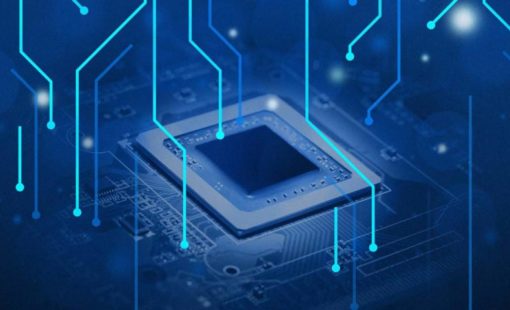
- Products
CR-8000 is a System-Level PCB & IC Package Design software including 3D Multi-board, Analysis and MCAD Integration
- Datasheet