There is one thing that all design engineers will agree on: creating and gathering all the required data for PLM is error-prone and can be a royal pain. We all understand the value of releasing our design data to the corporate PLM system but our design process dictates multiple release points, and each one has a different purpose and data requirements.
Checkpoint or Milestone Releases to PLM
There are multiple times during the design process when design data should be packaged and placed in the PLM system. The most frequent release type is a daily or weekly checkpoint. This entails packaging up the data for archival purposes. Another common release type is driven by a milestone such as a design review. Design reviews can be done through the PLM system given the number of potential stakeholders. This require a release package that contains schematic and board viewables and a current BOM at a minimum. Specifications, simulation results and various other documents may need to be provided based on the review type. When the review is completed, mark-ups, instructions and BOM changes need to be passed back to the design team.
Release to Manufacturing
The release to manufacturing process can come in at least three flavors: prototype, first article and full production builds. A release to manufacturing PLM package contains the schematic and PCB viewables plus the entire fabrication package for the board. Depending on your manufacturing process, your list could include fabrication outputs such as drill, ODB++, Gerber, fabrication and assembly drawings and of course a BOM.
These release points occur repeatedly throughout the design process and the release package content generation is typically a manual process..
Common Pitfalls
-
Are we sure that the design files used to generate the outputs are the latest version?
- Are the board, schematic and EBOM in sync?
- Are there procurement or lifecycle issues with any of the components used in the design?
- Have there been recent footprint updates that need to resolve?
- Have I produced all the required outputs?
- Is my process repeatable?
There’s a Better Way
An advanced engineering data management system such as Zuken’s DS-CR has much to offer and can help solve many of these issues. By incorporating vaulted work-in-progress (WIP) design data, you can overcome many of the more common pitfalls in the process:
- Ensure that the correct design files are in play. The WIP vault keeps the latest version current.
- Add approval controls to your design data. Design data can be reviewed and approved prior generating release packages.
- Provide an audit trail; you will always know who did what and when.
DS-CR’s intelligent EBOM is directly related to the schematic and board layout. These items are checked and kept in-sync throughout the design and release process. The EBOM is directly tied to your corporate component library allowing you instant visibility into any possible component lifecycle issues.
Document generation is automated and works directly on your vaulted design data. It is template-driven ensuring that each release point has all the necessary outputs.
Object-based notifications will inform you of changes that might impact the integrity of your design. Here are a few examples:
- A component library part changed after the schematic was last vaulted.
- There has been a footprint change after the board was last vaulted.
- There has been a schematic change after the board was last vaulted.
- The EBOM and schematic have been modified by different people.
As you can see, engineering data management systems such as DS-CR are essential to ensuring a smooth transition between your design process and PLM release points. The fact that you can fully trust content and source data will lower your risk and just might let you sleep better tonight.
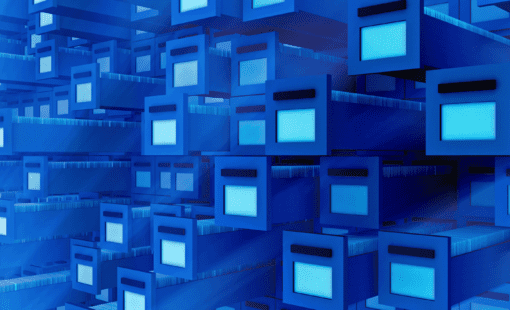
- Products
Data management for PCB (DS-CR) and electrical/fluid engineering (DS-E3). DS-2 is a mature, cross-disciplinary engineering data management platform developed in partnership with more than 3,000 leading companies worldwide.
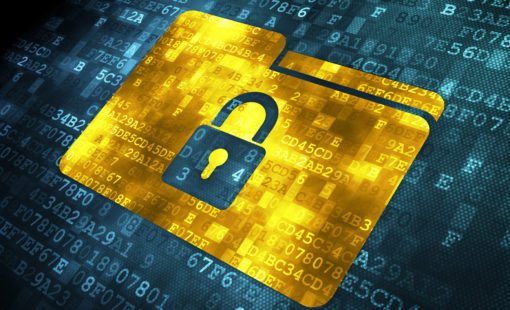
- Products
DS-CR supports the specific demands of PCB design data management. It combines multi-site library, design data, and configuration management capabilities into a unified engineering environment.
One Comment