Der Printed Circuit Board-Markt setzt sein kontinuierliches Wachstum fort. An der Spitze dieses Wachstums steht der Sektor der Flex-PCB-Designs (FPC). Viele Forscher sagen voraus, dass der FPC-Markt im kommenden Jahrzehnt jährlich um mehr als 10 % wachsen wird.
FPC ist eindeutig keine neue Technologie mehr, es gibt sie schon seit Jahrzehnten. Dank intensiver Entwicklungsarbeit und Innovationen der Werkstoff- und Leiterplattenlieferanten entwickeln sich die FPC-Technologien rasant weiter und ersetzen in vielen Designanwendungen Kabel und starre Leiterplatten. Je mehr FPCs in einem Produktdesign enthalten sind, desto kritischer werden die Kosten, ganz gleich in welcher Branche. Dies gilt insbesondere für die Massenproduktion von Produkten mit hohem Volumen, beispielsweise von Konsumgütern.
Flex PCB und Design for Manufacturing
Die Berücksichtigung von DFM-Anforderungen (Design for Manufacturing) während des Designprozesses verbessert die Qualität des Flex-PCB-Designs und trägt zur Effizienz der Hardwareentwicklung bei. Gleichzeitig hilft es, Änderungsschleifen zu reduzieren. CAD- und DFM-Prüfsysteme werden ständig weiterentwickelt, um mit den neuen Technologien Schritt zu halten. Aber ist es früh genug, um die FPC-Fertigungskosten zu berücksichtigen?
Diese Frage war die Hauptbeweggrund für die Untersuchung der verschiedenen Maßnahmen zur Senkung der FPC-Herstellungskosten. Die Frage weckte auch das Interesse an der Entwicklung von Design for Panelization (DFP).
Übrigens bietet das Advanced Design for Manufacture (ADM)-Tool von Zuken auch Vorteile im Bereich Flex-PCB-Design. Es handelt sich um eine GUI-basierte Engine zur Erstellung komplexer DFM-Prüfungen. Das Tool ermöglicht eine präzise Erstellung von DFM-Regeln, die auf FPC-spezifische Probleme eingehen. Aber das ist ein Thema für einen weiteren Blogpost.
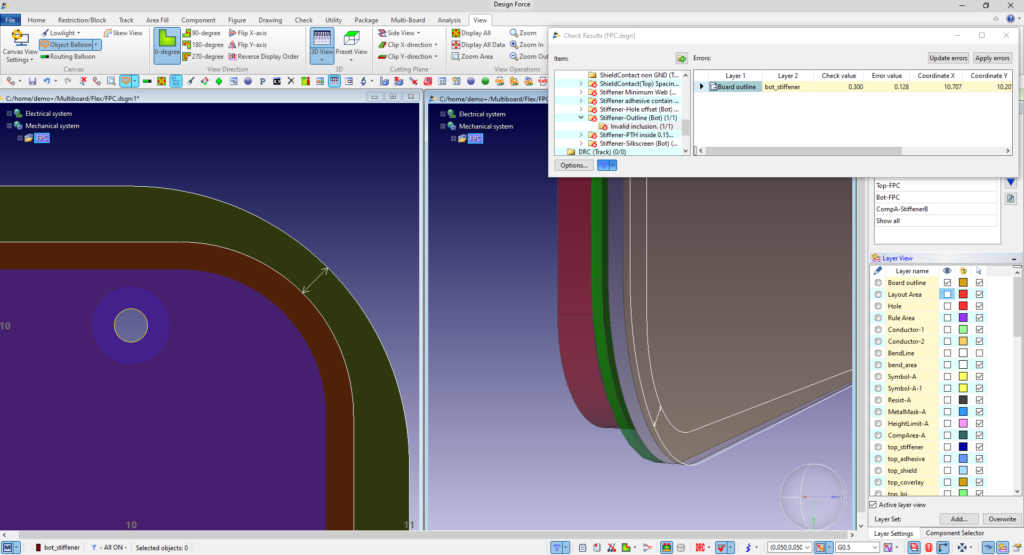
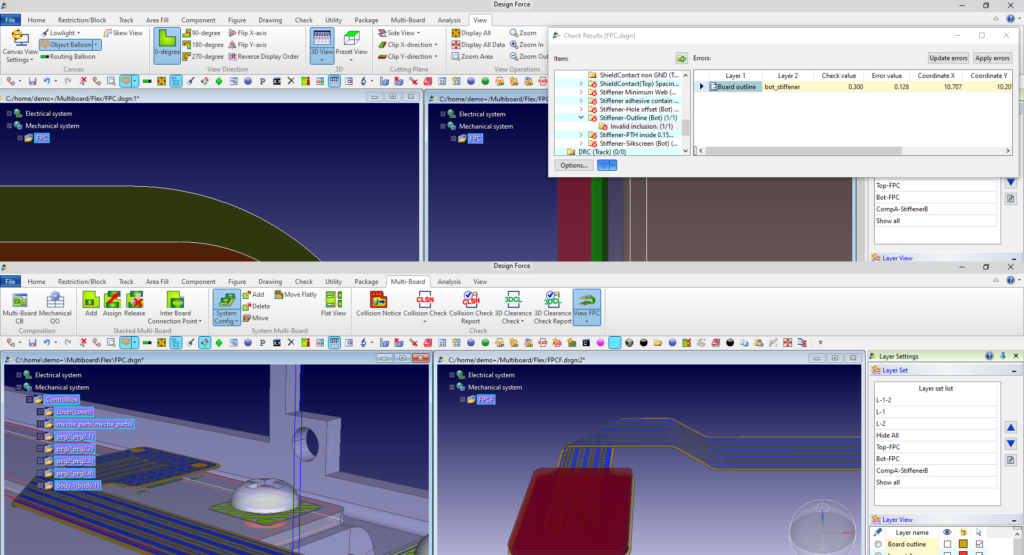
Kosten-Optimierung durch Mehrfachnutzung
Die bewährte und kostengünstige Single-Layer Flex Leiterplatte ist heute weit verbreitet. Doch die Nachfrage nach komplexen FPC – doppelseitig, mehrlagig und mit neuen Materialien wie LCP (flüssigkristalline Polymere) – nimmt stetig zu. Sie können sich sicher vorstellen, dass sowohl die Herstellungs- als auch die Materialkosten für komplexe Flex-PCBs relativ hoch sind.
Daher ist die Berücksichtigung der verschiedenen Kostenfaktoren für ein wettbewerbsfähiges Produktdesign und eine wettbewerbsfähige Fertigung von entscheidender Bedeutung. Durch frühzeitige DFM-Prüfungen im Entwicklungsprozess von Leiterplatten kann die Effizienz durch Einsparung von Schleifen zwischen Entwicklung und Fertigung verbessert werden. Beachten Sie jedoch, dass es auch wichtig ist, die direkten Materialkosten der FPC durch eine optimierte Materialausnutzung zu senken, um so die Kosteneffizienz zu maximieren.
Die Senkung der Materialkosten ist bei komplexen FPCs und bei der Massenproduktion von hohen Stückzahlen besonders wichtig. Eine der wirksamsten Methoden zur Kostensenkung ist die Verbesserung der Materialausnutzung auf den Produktionsflächen. Mit anderen Worten: Je mehr Platinen auf einer bestimmten Fläche untergebracht werden können, desto billiger wird die Platine sein. Da diese Mehrfachnutzung ein direkter Kosteneinsparungsfaktor ist, beauftragen die Lieferanten oft Spezialisten mit der Entwicklung der FPC-Platinen.
Diese Spezialisten entwerfen das Layout der Platinen präzise, um den verfügbaren Platz und die Materialausnutzung zu optimieren. Sie berücksichtigen dabei verschiedene Faktoren, wie z. B. Werkzeuge/Vorrichtungen, Formen, Stanzwerkzeuge, Folienversiegelung und natürlich die Fertigungsmöglichkeiten der Produktionslinien. Das Element mit dem größten Einfluss auf die Materialausnutzung ist jedoch die Platinenform, die bereits in den frühen Phasen des Produktdesigns festgelegt wird.
Design for PCB-Panelization
Vereinfacht gesagt, schlägt sich eine optimierte Platinenform auf die Materialkosten nieder. Es ist von entscheidender Bedeutung, die Platinenform unter Berücksichtigung der Ausnutzung des Plattenmaterials zu entwerfen. Doch wie lässt sich das bewerkstelligen? Bevor wir weitermachen, wollen wir die allgemeinen Annahmen für den Design- und Herstellungsprozess von flexiblen Leiterplatten bestätigen und uns dabei auf das Design for Panelization (DFP) und die damit verbundenen Kosteneinsparungen konzentrieren.
Allgemeine Grundlagen:
- Flex-Leiterplatten werden als Platten hergestellt, und jede FPC-Platine wird in einem bestimmten Muster mit einem bestimmten Abstand in der Platte angeordnet, das als “Step and Repeat” bezeichnet wird.
- Im Gegensatz zu einer starren Leiterplatte können Flex PCBs in jedem beliebigen Winkel angeordnet werden, wenn sie ein regelmäßiges Muster aufweisen, um eine effiziente Mehrfachnutzung zu ermöglichen (z. B. Formenschnitt und Folienlaminierung). Völlig unregelmäßige Layout-Muster sind daher für eine effiziente Verarbeitung tabu.
- Gleichzeitig müssen Sie aus Gründen der Herstellbarkeit bestimmte Abstände einhalten (z. B. Board zu Board) = 1,5 mm, X-Panel-Kantenrand = 2 mm, Y-Panel-Kantenrand = 3 mm).
- Eine bestimmte Platinengröße mit einer bestimmten Flex-Konfiguration (Stackup) hat feste Stückkosten.
- Ein Quadratmeter einer doppelseitigen FPC-Platine mit silbernen Abschirm- und Coverlay-Folien auf beiden Seiten, mit Bestückung in einem Bereich auf der Oberseite (d. h. FR4-Versteifung auf der anderen Seite und LPI-Maske auf der Oberseite) kann z. B. 200 $ kosten. Diese festen Stückkosten ändern sich nicht, egal wie viele Platinen pro Quadratmeter produziert werden.
- Mit anderen Worten: Je mehr Platinen pro Quadratmeter, desto billiger ist jede Flex-Platine.
- Änderungen am Grundruss der Platine sind in den frühen Entwurfsphasen möglich, später jedoch nicht mehr.
- Produktingenieure ( Systemplaner oder Maschinenbauingenieure) sind meist für diese Phase verantwortlich. Sie findet sehr frühzeitig im Entwicklungsprozess statt, möglicherweise sogar noch vor der PCB-Designphase.
Fazit
- Durch eine optimierte Plattenform lässt sich die Fertigungseffizienz verbessern.
- Die Form der Platine kann nicht mehr geändert werden, sobald das Design feststeht. Die Optimierung muss also bereits in einer frühen Phase erfolgen.
- Das Hinzufügen eines neuen Schrittes in der frühen Phase muss für Systemplaner, Produktingenieure oder sogar Maschinenbauingenieure schnell und einfach sein, um den Entwurf zu optimieren und What-if-Analysen durchzuführen.
Um auf die eigentliche Frage zurückzukommen: Wie entwirft man die Form der Leiterplatte und berücksichtigt dabei die Ausnutzung des Plattenlayouts? Die Antwort liegt in der Verwendung einer fortschrittlichen, automatisierten Designlösung. Zukens CR-8000 DFM Center ist ein Tool, das typischerweise von Leiterplattenherstellern für das CAM-Design verwendet wird. Es verfügt jedoch auch über ein Dienstprogramm namens FPC Panel Simulation Module. Dieses Dienstprogramm wurde ursprünglich für die Panel-Design-Spezialisten der Flex-PCB-Lieferanten entwickelt und ermöglicht die schnelle Durchführung von What-If-Simulationen der Panel-Konfiguration. Systemingenieure können es auch für PCB-Panelization verwenden, um das Leiterplattenprofil zu optimieren.
CR-8000 bietet einfaches Drag-and-Drop und kann mit wenigen Mausklicks Tausende von Layout-Mustern durchlaufen, um die Auslastungsdaten und das tatsächliche Leiterplattenlayout zu validieren – und das alles innerhalb von Sekunden oder Minuten (*1). Genaue Reports können überprüft werden, um die Dichte und Leiterplattenanzahl der Mehrfachnutzung schnell zu bestimmen und in den Entscheidungsprozess einzubeziehen.
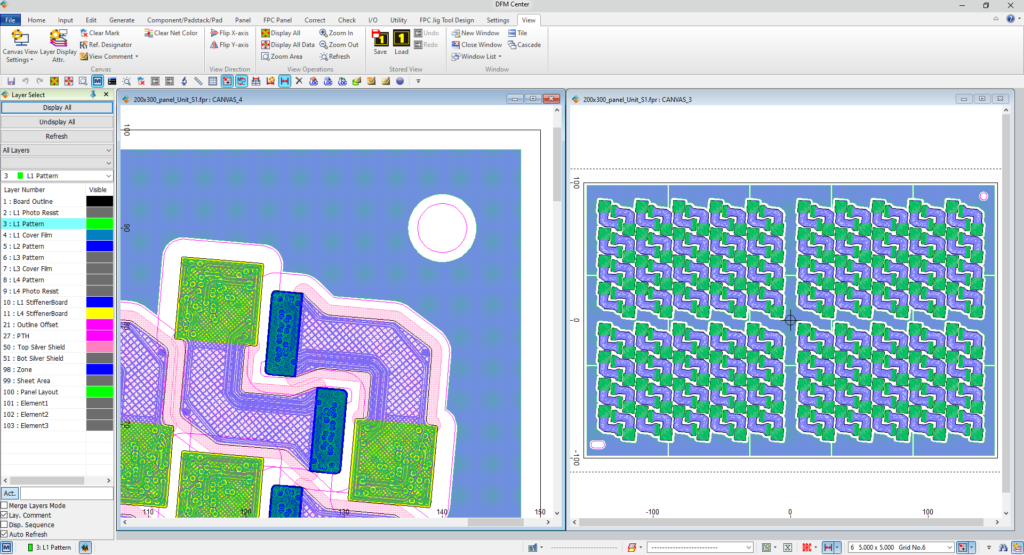
In der Praxis ist es zudem wichtig, andere Kostenfaktoren zu berücksichtigen. Dazu gehören Unterschiede bei den Lohnkosten, je nachdem, wo die Leiterplatten hergestellt werden, sowie die Betriebs- und Wartungskosten für die Flex-PCB-Produktionsanlagen. Man kann aber auch davon ausgehen, dass eine optimierte Mehrfachnutzung die Kosteneffizienz in diesen Bereichen verbessern wird.
Kostenreduzierung für unsere Kunden
Zuken hat dieses Tool auf der Grundlage von Kundenwünschen entwickelt. Die Senkung der Kosten für die Produkte unserer Kunden ist ein wesentlicher Aspekt, der den Großteil unserer Entwicklungsarbeit bestimmt. Unsere Kunden profitieren davon, dass sie mehrere Platinen-Konfigurationen durchspielen können, um bereits in einem frühen Stadium des Designprozesses die ideale Anordnung der Platinen zu finden.
Darüber hinaus können die Designer mit dem Tool verschiedene Flex-Formoptionen gegeneinander abwägen, um die perfekte Endform zu definieren. Durch die optimierte Form der flexiblen Leiterplatte und die Konfiguration der Mehrfachnutzung können wir sicherstellen, dass unsere Kunden jeder mögliche Cent in den Endprodukten der Kunden einsparen können. Wir freuen uns, Ihnen diese Mehrfachnutzung für Flex-PCB-Designs vorzustellen und Ihre potenziellen Kosteneinsparungen zu ermitteln. Bitte kontaktieren Sie uns für weitere Details.
*Abhängig von der Platinenform und den Simulationsparametern.
Weitere Informationen darüber, wie Sie die Produktivität der Flex-PCB-Fertigung durch bessere DFM-Prüfungen steigern können, finden Sie in unserem On-Demand Webinar: