Man-carried military communication systems often consume large amounts of power. The heat must be removed from the electronics package to avoid frying sensitive electronic components. The package typically is designed to be carried in a backpack which often puts difficult constraints on the form factor and weight of the system. A military system integrator approached Additive Design Consultancy with the challenge of providing a thermal management solution for a 14 by 10 by 5 inch system. The difficulty of this application was increased by the fact that the printed circuit boards (PCBs) that generate most of the heat are mounted on one of the 14 by 10 inch surfaces, yet to maintain the proper form factor, the external fans cannot be mounted on that surface. Another challenge was that the package must be relatively thin and light in order to fit into the backpack of the soldier who carries it on the battlefield.
In this case, the original design for the package was a machined aluminum box with external fans. “Before sending us this project, our customer had previously talked to several design consultancies that had determined that the interior of the package could not be cooled simply by transmitting heat through the solid aluminum walls of the device,” said Adam Arnold, Director of Additive Design Consultantcy. “Liquid cooling provided a potential alternative, but a conventional liquid cooling solution would have driven up the cost and weight of the package.” Additive Design Consultancy specializes in exploiting the new design rules offered by additive manufacturing to push past existing structural, fluid and thermal performance boundaries. In this case, Additive Design Consultancy engineers had the idea of printing the walls of the package with internal cooling channels that can be filled with a liquid coolant that efficiently conducts heat to the heat sinks mounted on adjacent walls.
The system integrator provided Additive Design Consultantcy with the thermal and structural requirements for the package. Additive Design Consultancy engineers took advantage of the design freedom provided by additive manufacturing by starting from blank space and iterating to an optimized design. Their objective was to leave as much room as possible inside the walls of the package for a cooling channel while meeting the structural and weight requirements. They took advantage of the design freedom offered by additive manufacturing to ignore manufacturability rules such as maintaining walls of uniform thickness, avoiding internal voids, etc.
Additive Design Consultancy engineers defined the starting geometry with an external shape including mounting surfaces as defined by the systems integrator then used engineering judgement to remove material from the interior of the rectangle. They carefully checked each proposed design to ensure that the interior void is contiguous and that the final part shape is able to support the loads provided by the system integrator. They defined two types of lattice structures including a square column-based lattice for the larger wall that mounts the PCBs and an X lattice on the adjacent walls. The engineers evaluated hundreds of possible design configurations while iterating to a design that provides the best possible thermal performance within the required geometrical and structural constraints.
“Additive manufacturing provides virtually limitless design freedom, making it possible to build very complex heterogeneous structures that would be too expensive to produce with conventional methods,” Arnold said. “In this case, additive manufacturing made it possible to provide an internal cooling system without paying a cost penalty compared to a much simpler structure. The end result is a package that dramatically improves thermal management performance while meeting structural requirements without an increase in weight. The use of liquid cooling to conduct heat from the PCBs to the external fans reduces the maximum temperature inside the box from 125F to 96F. Even greater thermal performance could have been achieved by using an external lattice on the package to increase the surface area of the package which in turn would have increased heat transfer to the air.”
Related Content
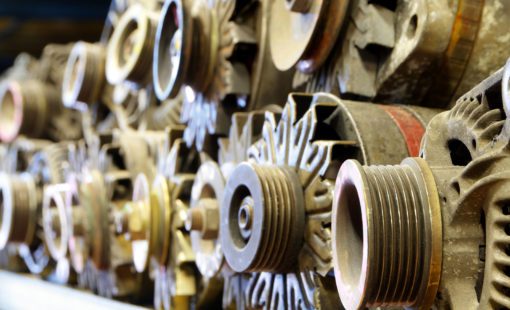
- Blog
It has often been noted that many of the aircraft and other weapons systems used by the armed forces are older than the service men and women operating and maintaining them. While the average age of a U.S. domestic commercial airliner is 11 years, it is not uncommon for aircraft to still be in service at 30 years. Likewise, there are many machines and systems in electric power generation, discrete parts manufacturing, chemical process, oil and gas production and many other industries that have been in continuous operation for several decades or longer.
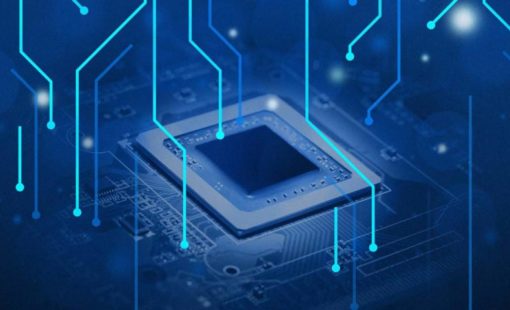
- Products
CR-8000 is a System-Level PCB & IC Package Design software including 3D Multi-board, Analysis and MCAD Integration