In my previous post in this series about effectively reusing design modules to increase product quality and decease development time, I challenged you to think about how well you’re making use of existing design modules and why getting better at this could be a competitive differentiator. I looked at some of the design challenges circuit designers are facing, such as miniaturization, proliferation of electrical constraints and high speed design requirements, as well as some of the potholes it’s easy to fall into when working with modular design.
Today I’m going to take a step-by-step look at some circuit module reuse best practices, along with an example. The answers that I’ve kept you waiting for in part 1.
Managing modular circuit blocks
An increasingly popular and effective way of dealing with human errors creeping in when reusing designs (such as inadvertently using older block prior to an issue being resolved) is by using data management software that stores reusable circuitry as modular blocks. This greatly simplifies the process of reusing existing PCB schematics, parts lists and layouts.
The new generation of data management software controls access to circuit blocks, so only authorized editors can make changes. Editors need to check out the modular block and other users can’t make any changes to it until it’s checked back in, to ensure the design integrity. The software can also be configured to require approval when a change is made to a modular block.
Reusable modular blocks can be created in two different ways:
Top-down approach
- Partition the design early on in the design process.
- Create the block diagram, then add circuitry to each block.
- Validate blocks and complete the design.
- Register the parts list, schematic and layout of each block in the data management system, along with its metadata containing detail such as which products the block is used in, engineers involved in its design, and the approval chain.
Bottom-up approach
- Create and validate the circuitry .
- Partition the design into blocks.
You can see how much more effort the top-down approach takes (four stages rather than two), and it requires more planning time. But the payoff is huge in that blocks produced this way are usually much more suitable for reuse, so you save lots of time later on when you reuse the blocks in variant designs. Put the work in at the start to reap the benefits later on down the line.
Streamlining the design process – cell phone example
Let’s look at how the modular design approach can substantially help streamline the design process for the cell phone example mentioned in part 1. We’ll assume that the design has been partitioned into blocks representing the RF, baseband, Wi-Fi, Bluetooth and other sections.
The engineer working on the new variant follows this simple process:
- Call up the modules by searching the data management system for the product name.
- Check the documentation stored in the system for each module they want to use, to ensure it is a good fit for the new design.
- Drop the modular blocks into the new design. The parts list, schematic and layout of each modular block will all be incorporated into the new design.
- Design the new RF block and any other new blocks needed, either from scratch or by modifying existing blocks.
- Connect sections together and route new areas of the design.
- Check the design
- Check for issues such as signal integrity and thermal management, focusing on the newly-routed areas.
- Do a basic simulation of the complete design; even though checked modules are used, there’s a small possibility combining them could cause an issue.
By designing this way, regulatory compliance time can be reduced by using proven design blocks. This reduction in design time means it’s possible to bring products to market faster, which helps increase revenue and enables new products to gain market share before they face serious competition. Modular circuit reuse also reduces errors by allowing designers to use proven designs wherever possible.
Is now a good time for you to make best use of modular design to help your team develop and release boards faster?
Learn more about engineering data management here, and view our webinars.
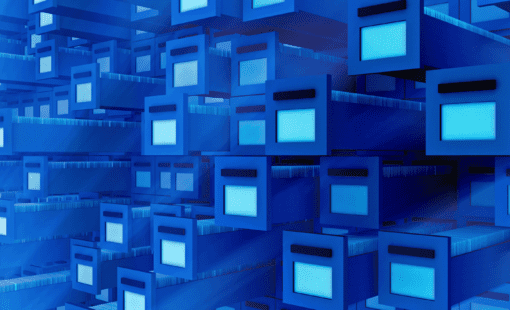
- Products
Data management for PCB (DS-CR) and electrical/fluid engineering (DS-E3). DS-2 is a mature, cross-disciplinary engineering data management platform developed in partnership with more than 3,000 leading companies worldwide.
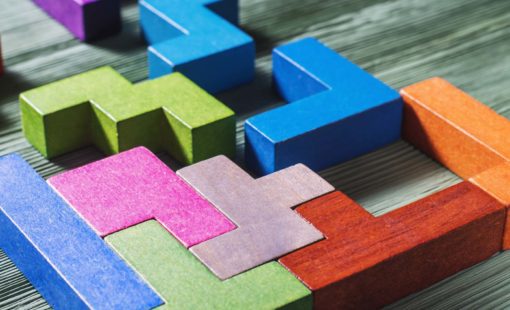
- Solutions
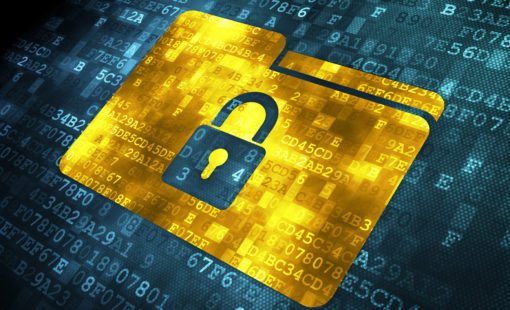
- Products
DS-CR supports the specific demands of PCB design data management. It combines multi-site library, design data, and configuration management capabilities into a unified engineering environment.
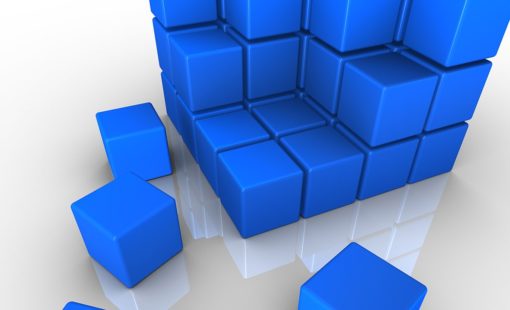
- Blog
In this two part series of blog posts, I’m going to be looking at reuse with modular design in PCB development, and how you can streamline your methodology to reduce design time, reduce design errors and increase product quality.