New Products
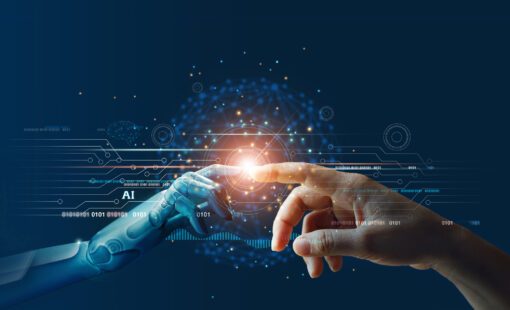
- Products
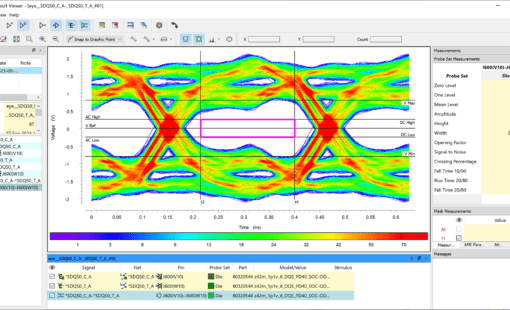
- Products
CR-8000 includes fully-integrated simulation and analysis tools to verify all aspects of your single or multi-board designs
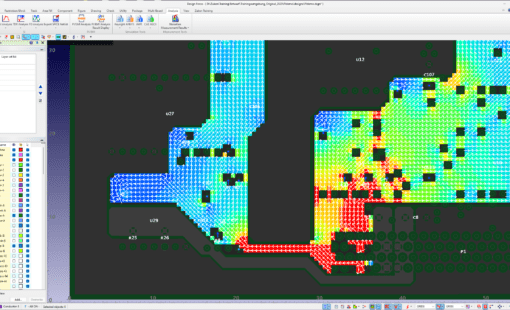
- Products
CR-8000 includes fully-integrated simulation and analysis tools to verify all aspects of your single or multi-board designs
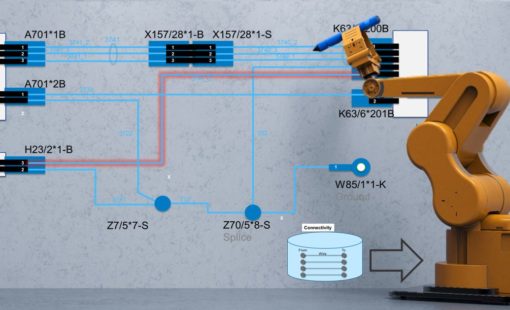
- Products
E3.ConnectivityBrowser - Automatically visualize connection information as circuit diagram representations
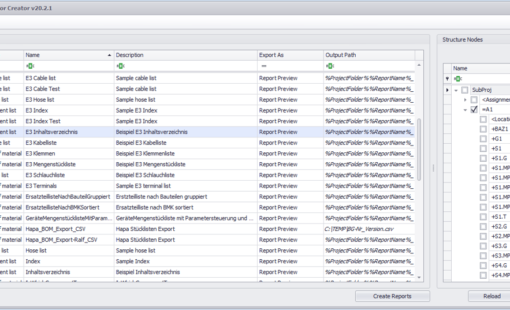
- Products
The E3.ReportGenerator is a free tool for creating customised reports from E3.series projects in a few simple steps. These reports can be configured according to various parameters and exported in various formats. The tool requires no licence and can be launched directly from within E3.series.
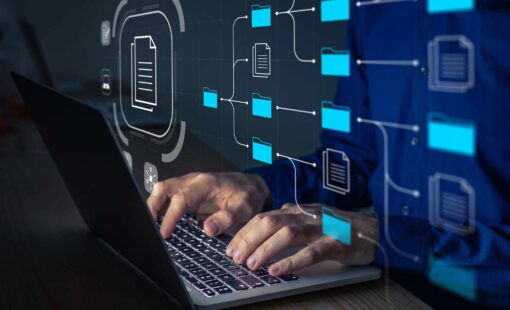
- Products
GENESYS is an integrated model-based systems engineering software toolset that covers all four domains of systems engineering — requirements, behaviour, architecture, and verification and validation.
New Releases
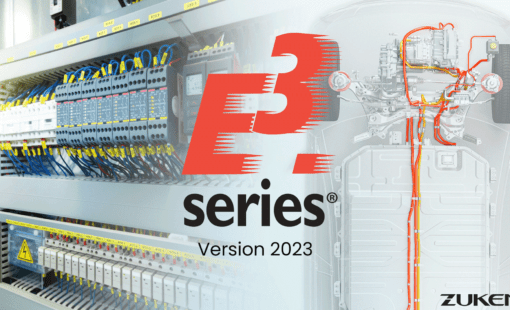
- Products
E3.series Release 2023 - an overview of the most important new features
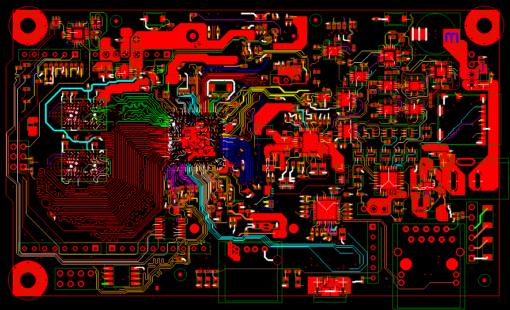
- Products
CR-8000 Release 2023 includes enhancements to support design efficiency and analysis, enabling users to tackle the challenges of high-density, high-speed PCB designs. A specific focus was given to reorganizing and extending CR-8000's comprehensive range of signal integrity, power integrity, and EMC analysis tools, now packaged in the configurations of CR-8000 Design Force Analysis Advance.
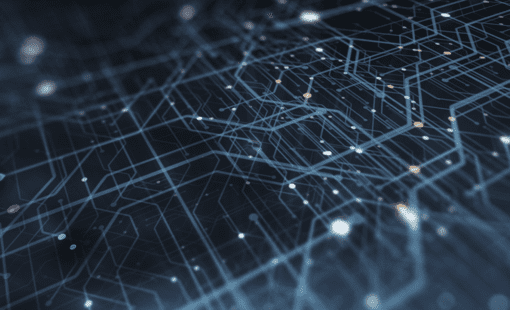
- Press Release
GENESYS 2023 includes improved capabilities for storing, organizing, and managing views.