In my last post (Pre-Layout Analysis Phase for High-speed Designs, Part 1), we discussed why we need to perform pre-analysis and how to use the pre-layout analysis features in Zuken’s CR-8000 Design Gateway and Design Force. This post continues the discussion, focusing on using a constraint-driven methodology in the pre-layout analysis phase.
The pre-layout analysis phase serves as a process gateway from a design to a product. It helps validate if a design is stable, functional, and cost-effective. The pre-layout analysis phase also defines the PCB design rules (routing layers, skew, length, impedance control, and more). Moreover, it establishes the signal integrity rules for high-speed products (signal level, delay, eye opening, overshoot/undershoot, power/ground voltage drops, crosstalk noise, and more).
How Can a Constraint-Driven Methodology Help?
High-speed PCB design is complicated. Often, malfunctions or defects in the board don’t show up until after the product goes to production. Mistakes equal money! So to eliminate these potential issues, design engineers and analysis engineers need to create a series of rules–or constraints–for PCB layout engineers to follow. These constraints will help them avoid possible mistakes early in the design process before a board goes to production.
PCB layout engineers also need the ability to provide feedback if there is a constraint that cannot be satisfied. For example, spacing, routing, layer arrangement, etc. This feedback process is often tedious and labor-intensive since it involves moving data and back and forth through multiple cycles. Using a constraint-driven methodology within a unified design environment will streamline this process.
The Complete Constraint-Driven Environment
A complete constraint-driven PCB Design environment will include the following:
-
Consolidated Constraint Environment
- Consolidate your design intent into your CAD data for both schematic and layout designs, and everyone in the various design and analysis phases can stay in sync seamlessly.
-
Intuitive Constraint Data Post
- Provide a simple list, color-coded, changeable, sortable interface for constraint entry and management.
-
Template and Simulation-Driven Rules
- Ensure the PCB routing structure stays as you want with topology template rules; then define constraints directly from simulation results for design optimizations.
-
Real-time Feedback and Verification
- Working with a real-time DRC engine to provide immediate constraint pass/fail feedback in the design process, enabling adjustments on the fly.
-
Design Context Evaluation
- View and evaluate the requirements in the design context to ease the review and change process.
-
Comprehensive Reporting
- Quick analysis and automatic report generation for signoffs.
A constraint-driven system needs an interface that can loop the constraints from pre-analysis to PCB layout, then on to post-layout verification, and the other way around. Zuken’s CR-8000 Constraint Browser has all of these capabilities and is THE interface to use for constraint-driven purposes.
CR-8000 Constraint Browser
CR-8000 Design Gateway schematic tool and CR-8000 Design Force PCB layout tool share the same Constraint Browser for data exchanges. The Constraint Browser allows users to set up the constraints in both tools, then perform forward and back annotation and cross probing between Constraint Browser and Design Gateway or Design Force.
The Constraint Browser in Design Force uses the exact same interface as the one in Design Gateway. Also, the Constraint Browser in Design Force has greater content feedback from PCB routing results. Given that Design Force is a PCB layout tool, the user can access reporting on impedance, delay, routing length, skew, etc., for real-world PCB design and verification.
Conclusion
The pre-layout analysis phase is essential across the entire process for high-speed PCB designs. It determines if your design is implementable, stable, and cost-effective. At the same time, it allows the designer to explore options before making final design decisions.
Pre-layout analysis has the duty to give the constraints for PCB layout in the process. The Constraint Browser inside the CR-8000 tool suite enables a simple, intuitive constraint-driven methodology with real-time feedback and comprehensive reporting for even the most challenging high-speed PCB designs.
In my next post, we will discuss the routing functions required for high-speed PCB designs. Stay tuned!
References
Related Products and Resources
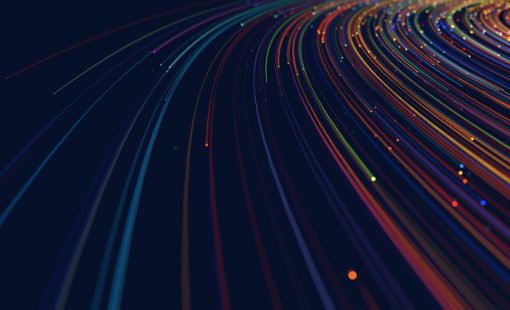
- Blog
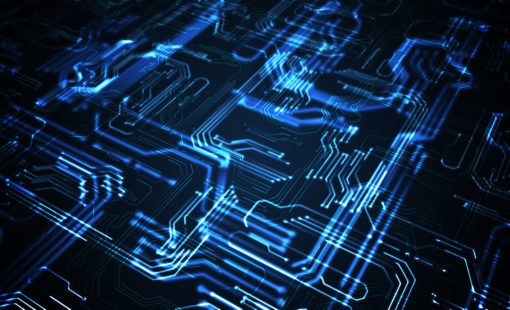
- 2020 Technical Webinars
This webinar will explore a high-speed design process in CR-8000 that utilizes a constraint browser, topology template, crosstalk estimation, signal and power integrity simulations.