In this two-part series of blog posts, I’m going to be looking at reuse with modular design in PCB development, and how you can streamline your methodology to reduce design time, reduce design errors and increase product quality.
The electronics industry has been doing it for decades. Software development too.
Although we’ve been talking about it for years, in PCB design it has yet to catch on in quite the same way despite there being a host of benefits to be reaped from modular design practices. So in the first of this two-part series, I’d like to challenge you to ask yourself a few questions about how you reuse designs:
- Are you reusing as many of your designs as possible?
- Are you getting some benefits from reusing designs… but inadvertently creating new problems?
Some of the benefits of reusing PCB modules for common functions, including:
- Avoiding potential signal integrity or thermal problems by using circuit data with proven performance.
- Reduction in time taken for schematic capture and PCB design leading to a reduction in development costs.
- Fewer design errors.
- Ultimately, helping bring quality products to market faster.
Circuit design issues
In fact, efficient reuse is one of the key methods that companies are leveraging to become more competitive and keep up with the volume and frequency of new product introductions. The keyword here is ‘efficient. You may be reusing some elements of your designs, but it’s being able to do it effectively that’s going to increase quality and improve your development process.
Reuse is getting more attention because much of the electronic content in electronics products have been commoditized, increasing amounts of functionality becoming consolidated in application processors or system-on-chips (SoCs) and their reference designs. Standardization of busses and protocols allows for even more reuse. Other factors include:
- Proliferation of electrical constraints.
- Stricter-than-ever requirements to maintain reliability.
- Manufacturability and compliance.
- Challenges using IC and field-programmable gate array (FPGA) for high-speed design.
Current circuit reuse methods
When you need to produce a related product you might often copy and modify the original design, or use predefined modules from the original design. For example, a new cell phone variant might reuse the baseband, Bluetooth and Wi-Fi modules, combined with a new RF section.
But you can run into some potholes with this approach.
The perils of human data managers
In larger design teams, it can often be difficult to find a related design that fits the specific requirements of the current project, it’s a classic case of you can’t see the wood for the trees – sound familiar? There’s always the potential for the designer to inadvertently reuse a version of a related design that doesn’t include the latest changes.
Other issues that the cut and paste method can lead to include:
- Knowledge developed in creating the original design is typically lost. The copied blocks lack intelligence such as the underlying design methodology and best practices.
- Traceability – sometimes only one person knows the source of individual modules, so if a problem is discovered later on the designers of the new module may not even be aware of the change. The original error will be replicated and there’s the risk it may not be caught before the product is released, or that large costs are incurred by late-stage design changes.
Ouch, these kinds of problems hurt. So now we’re on the same level, you know I’m with you there understanding the pain, I’m afraid I’m going to keep you hanging on a little longer, for the answers in part 2, where I look at methods for managing circuit modules, design best practice, and an example of streamlining the product design process.
In the meantime, you might like to check out Zuken’s Design Force PCB design software.
Back soon…next week is my deadline, so I won’t keep you dangling for long.
Related Products and Resources
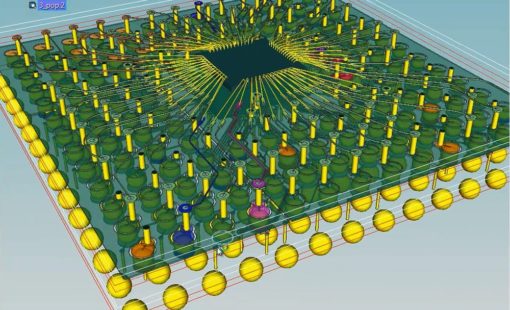
- Products
Design Force offers an intuitive, integrated environment for designing single and multi-die packages for wire-bond, flip-chip, and high density advanced packaging. Designers can start designs with early prototype input of chip and package data from the library, reuse data from IC layout tools, and take advantage of parametric wizards to streamline the creation of the system
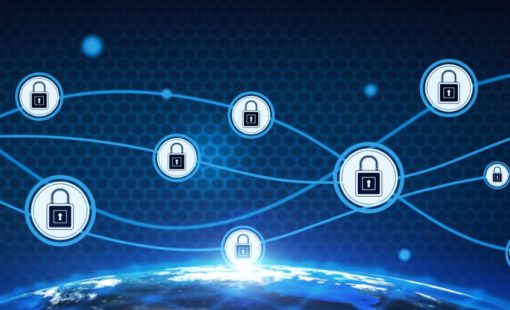
- Products
Zuken’s engineering data management platform DS-CR has been created to support the specific demands of PCB design data management. It combines multi-site library, design data and configuration management into a unified engineering environment.
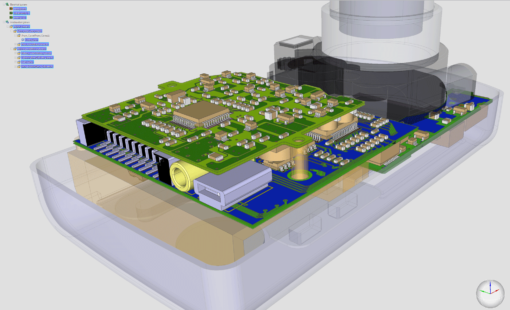
- Products
Design Force combines traditional 2D design with native 3D design and the latest human interface techniques, accelerated graphics and almost instantaneous rendering and refreshing. It is the fastest, most effective PCB design solution available today. Design Force enables design teams to layout their designs in the context of a complete system or product.
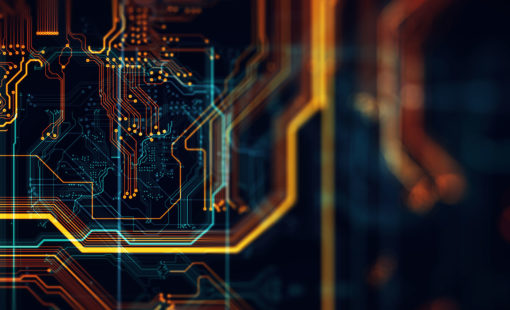
- Products
Building a competitive product today is much more difficult than a few years ago. Existing PCB-centric design processes are limited to a single PCB and do not provide the necessary tools for today’s competitive product development environment. PCB-centric design processes are falling behind.