Organizations will have to contend with an acute shortage of qualified staff in the coming years. The German Ministry of Economics sees the demographic change in the workforce as a growing business risk for companies, which as a result will have to cope with a significantly changed environment in the coming decade. The transition between generations, with more employees retiring than are coming out of universities and schools, will result in vacancies not being filled with skilled workers – especially in the fields of mathematics, information technology, natural sciences, and technology.
According to a recent VDMA survey of around 570 HR managers, the majority of respondents already see bottlenecks in almost all employee segments.
Proximity to customers, unparalleled innovative strength in research and development, and a high priority on schedule and quality still make local production attractive compared to offshoring, but competition from low-wage countries is increasingly exacerbating the situation in the German machinery industry. A strategic approach to digitization and automation can help to address the challenges posed by increasing complexity and a shortage of qualified workforce and to achieve cost-efficient and local production.
The challenge of electrical cabinet building
The field of tension is currently characterized by increased price pressure and, at the same time, growing quality demands and the desire for customization. In addition, the shortage of qualified specialists is increasing, particularly noticeable in control cabinet building.
Many steps in the production of control cabinets are still carried out by hand, for example, the processing of housings or wiring. When qualified technical personnel is lacking, the automation of production steps can help to free up capacities assigned to these tasks and thus increase production efficiency through the systematic use of their limited availability.
The basis for any automation is the digital twin of a control cabinet, which is continuously evolving throughout the entire planning and manufacturing process and fully represents the latest state of its data. The digital twin is the basis for all engineering and manufacturing processes, from mechanical wire processing and guided wiring to fully automatic wiring of pre-assembled terminal rails.
Modern ECAD tools, such as E3.wiringCockpit, provide digital support for control cabinet wiring on a mobile device. The routing path in the control cabinet is highlighted and all additional information relevant for an operator is displayed.
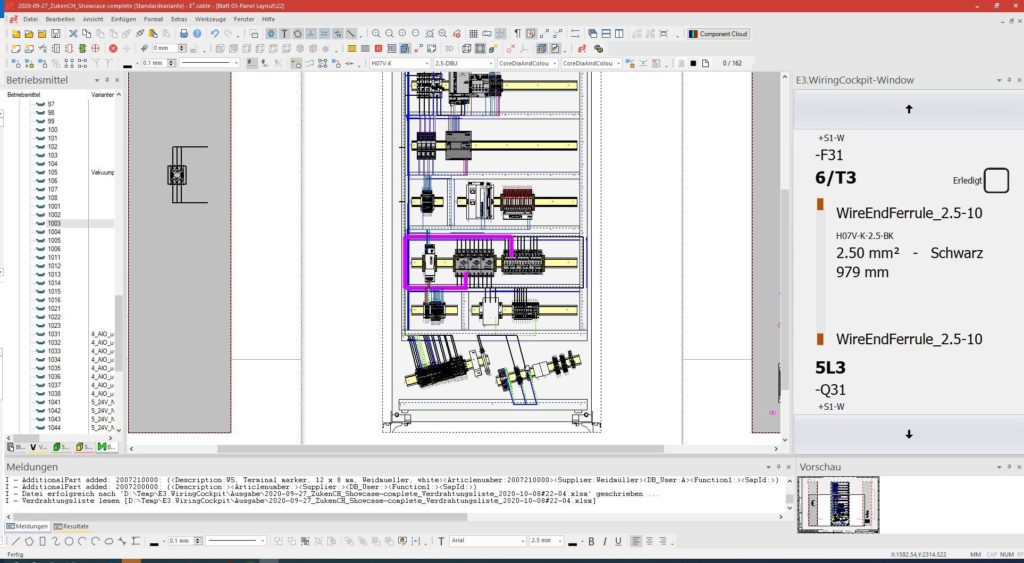
Deploying specialist skills in a strategic way
Hermann Nagel, Managing Director and Head of Sales at nVent Hoffman, clarifies: “The idea of automation is not that it replaces qualified staff, but that their capacity can be utilized in a more targeted and considerably more efficient way. Automating certain production steps not only increases efficiency but also leads to greater job satisfaction and less fluctuation in companies.”
Modifying housings and mounting plates takes a lot of time. With the nVent HOFFMAN ModCenter, the time-consuming machining can be automated with cutouts, drilling, and tapping. One or more cabinets, control panels, or mounting plates can be placed in the mounting system at the same time if required.
In our recent webinar, we will show these and other levers for optimizing production workflows and tools so that you can adapt your processes to face the challenges of the shortage of qualified workers in control cabinet manufacturing.
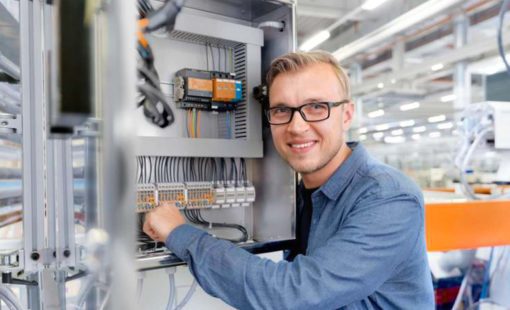
- Webinar
In this Smart Cabinet Building webinar, you will learn how to address the challenge of the shortage of qualified workers in control cabinet building by optimising seqences and tools for tomorrow's production
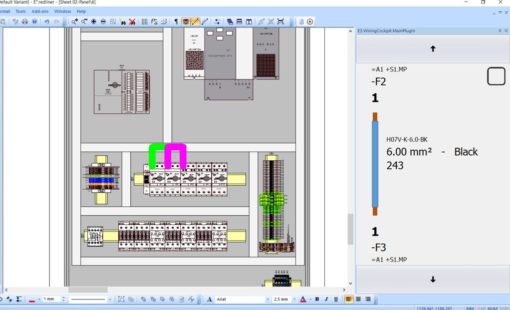
- Products
E3.WiringCockpit enables the display of wiring paths and connection information on mobile devices.