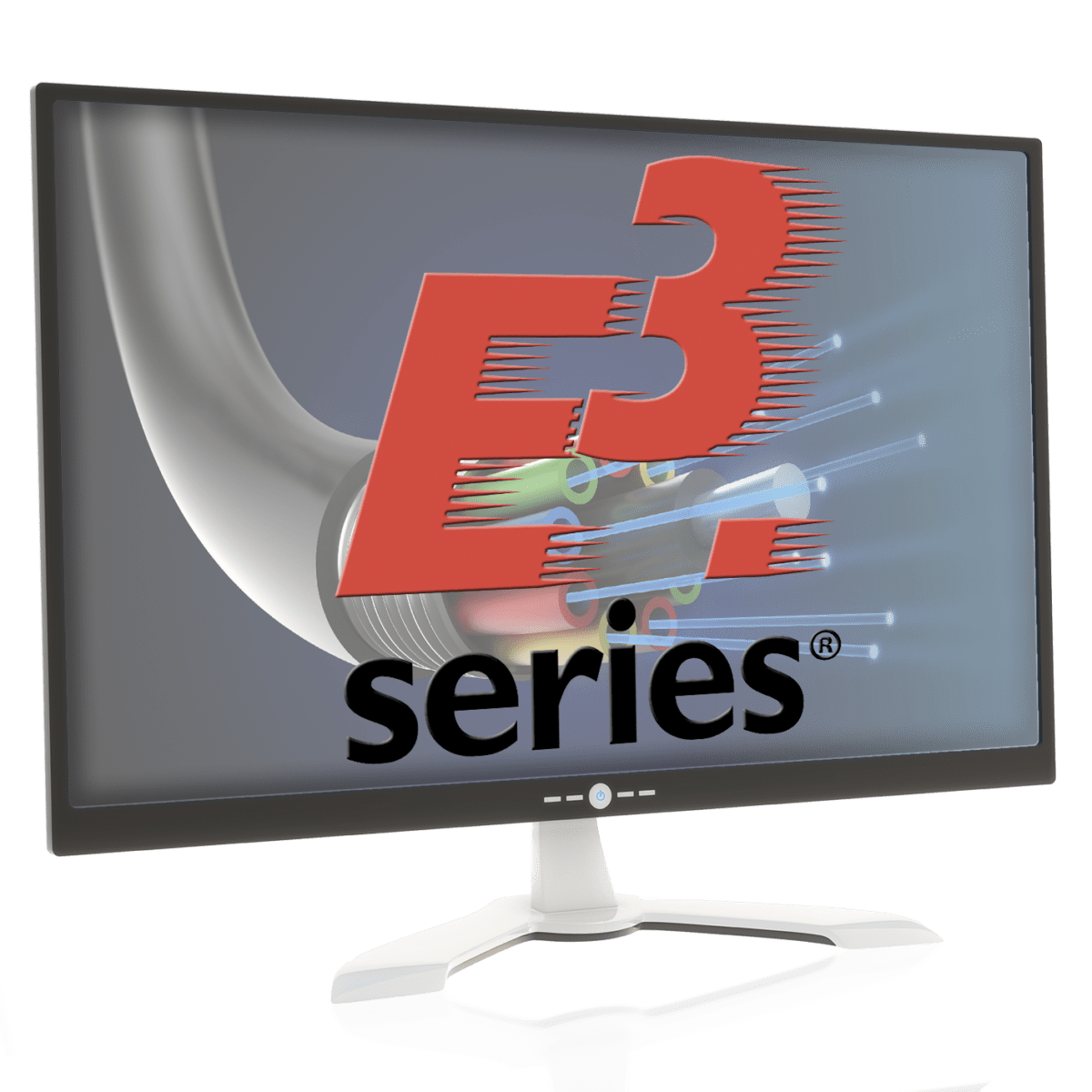
Zuken Offers Improved Productivity and Enhanced Collaboration with Latest E3.series Release
30 June 2015 – Munich, Germany and Westford, MA, USA – Zuken announces improved overall productivity for electrical design, plus sector-specific enhancements for automotive and manufacturing. The latest version of E3.series – Zuken’s industry-leading electrical and fluid CAD software – contains enhanced automotive design collaboration with E3.HarnessAnalyzer; ease-of-use improvements for design changes in the machinery sector; plus across-the-board productivity enhancements.
E3.series benefits from years of development and collaboration across a wide range of sectors with customers such as ARM Automation, which designs, builds and supports custom automated manufacturing systems.
The intelligence contained in the database of E3.series has helped reduce design time to about one-third of that required in the past. These time savings have made it possible for us to bid on more complex systems without concern that the electrical design could not be completed within the project deadline.
Increased productivity with improved handling
The growing number of options and variants offered for the automotive, industrial machinery and equipment sectors in particular means that additional management functions are necessary for schematics. E3.series is widely adopted across a broad range of industry sectors that need to handle options and variants both on authoring level, and as part of a larger data and workflow management system. On the authoring side, new E3.series functions that allow options to be sorted in ascending or descending order, as well as grouped by option packages and configurations, are welcome productivity improvements. Structuring the variant/option tree by arranging options below folders with user-defined names enables the user to assign, re-assign, find and structure options according to their intended use.
Other productivity benefits include:
- Automatic signal name generation based on the sheet and grid location, and the attributes of the device pin.
- Improvements in core management – defining and changing core connections is easily accomplished by selecting source and destination pins, saving a large amount of time when re-assigning core connections.
- New cabling tables simplify editing cable connections and identifying unconnected or partially connected cable connections. Manufacturing information can be directly assigned to the cables.
Enhanced automotive design collaboration
Improved connectivity is available between E3.series and E3.HarnessAnalyzer, a powerful new collaboration tool for viewing and analyzing harness drawings in the HCV (harness container for vehicles) data format, a widely used standard in the automotive supply chain. The graphical view and the physical data model reflected in various tables are now linked together. The whole harness can be analyzed and checked for bundle size, wire routing, used components, option assignment, weight and cost.
Other enhancements include automatic pin terminal functionality in E3.cable and E3.formboard. Connector pin terminal symbols represented in a cable or formboard drawing are switched automatically when exchanging a component or updating in the project.
Transparency and visibility in 3D with E3.panel
New transparency functionality makes working with complex 3D assemblies much easier. With a single mouse click objects can be made transparent or invisible, so walls or components can be faded out when, for example, multi-level cabinets are designed.
In E3.panel, 3D designs can be used to create 2D manufacturing drawings of every side of the cabinet. The 2D projection of the 3D design is created as an intelligent view. All modifications made in the 2D projection are reflected automatically in 3D, and vice versa.
Comprehensive manufacturing support
Finished designs in E.series contain all the necessary manufacturing information to build a cabinet or wire harness. In E3.series 2015 standard manufacturing outputs have been improved. The interfaces to strip, cut and mark machines (e.g. Komax) and to drilling and milling machines now contain additional information, such as data outputs for automatic bundling and labeling of wires, as well as the wire-end treatment.
For more information see www.zuken.com/e3series
– ends –
Related products
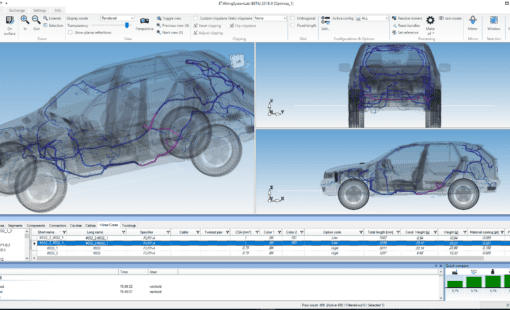
- Products
Sharing comprehensive harness design models and documents with internal or external project teams.
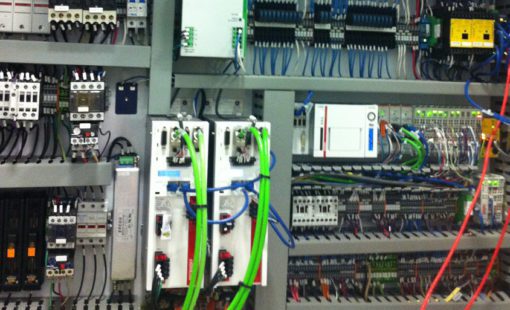
- Case Study
ARM Automation designs, builds and supports custom automated manufacturing systems for a wide range of industries. The electrical design of these systems can be complex, running up to several hundred drawing sheets. Using E3.series intelligent schematics to drive the electrical design process, the company has reduced their development time by two-thirds.
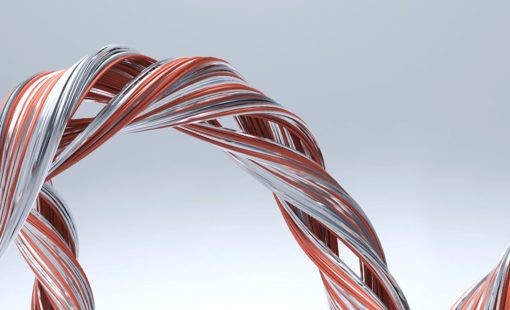
- Products
E3.series is a true concurrent electrical engineering environment supporting advanced requirements for electrical documentation, cabinet and wire harness design and manufacturing outputs.