COVID has not only been disruptive to our daily lives but now we’re seeing the effects on our work lives as well. Company operations have had to adapt to accommodate a workforce suddenly no longer in the office. Companies are facing new challenges, from remote tool access to the purchase and distribution of new online tools. Infrastructure is often the culprit behind many common difficulties. For example, using a tool license from home or gaining access to documents behind a firewall. Most IT departments have resolved the infrastructure challenges at this point and people are working again. But is the work getting done? Is product development happening? Or is the product development process infected?
Let’s take a look at the processes associated with electrical and electronic product development. Those activities traditionally require design teams to be located close to one another, or at least easily accessible (i.e., in an office). They’re also heavily reliant upon documentation. But traditional is no longer always practical. Since COVID, working from home has become the norm, and many of those document-based processes are now causing problems. Walking down the hall to ask a colleague a question has now become an email exchange with a probable meeting invite to follow. As a result, it seems like things are taking two to four times longer than pre-COVID. Is COVID the perfect catalyst for change and the adoption of the Digital Transformation? We think so.
Document-based processes are high risk
On an individual level, COVID manifested the term and behavior of “social distancing.” On a business level, it has essentially imposed the same distancing effect. There is stress on today’s product development processes, to begin with, given growing product complexity and the usage of documents wrapped in manual processes. Having design teams dispersed across buildings, states, or even countries is one thing, but adding social distancing in the workplace in addition to working from home exacerbates the situation. Therefore, there is no doubt that projects are taking longer to complete.
Today’s complex products require multiple design teams to collaborate extensively for long periods. Passing around spreadsheets or Visio files as the foundation for collaboration is prone to error on so many levels. Now is the time to embrace the digital transformation.
Digital transformation is the remedy
A digital transformation describes the adoption of digital technology to transform businesses and services. A recent IDC study reports that 90% of small- and medium-sized businesses are budgeting for the digital transformation. Surprisingly, the main goal is to improve product development and design processes. That suggests that companies have concluded that document-based processes can’t keep up and it’s time for a change. We couldn’t agree more.
Digital engineering is a derivative of the digital transformation and zeros in on product development. Digital engineering has three foundational components necessary for implementation:
- Model-based design
- 3D detailed design tools
- A digital thread
Deployment of a product development process built on these foundations would have been resistant to the COVID impact. A model-based approach, as opposed to Visio and unintelligent spreadsheets, provides a relationship-based description of the product and verification requirements. Detailed design teams work within a design envelope described by the model. And the communication backbone for negotiation, discussion, and approvals is the digital thread. Better communication and location independence is an effective way to battle the COVID physical distancing mandates.
Take your medicine
If COVID has had a significant impact on your business and, more specifically, your electrical and electronic product development processes, it may be time to swallow hard and make some changes. Document-based development processes have inherent communication challenges that are amplified by COVID. A model-based digital engineering process with 3D detailed design tools, combined with a robust communication backbone can prove resistant to COVID mandates and address growing product complexity. 90% of small- and medium-sized businesses have started budgeting for digital engineering to achieve product development improvements. If your product development process is infected with COVID, digital engineering is the remedy.
To learn more about digital engineering, check out these three webinars:
Related Products and Resources
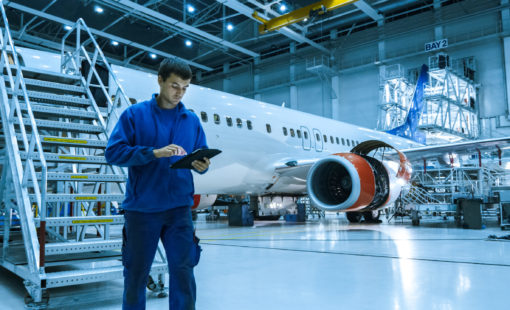
- Products
The Digital Thread is a foundational element of a successful Digital Engineering implementation. Digital conversations involving procurement, design, manufacturing and field service replace email and paper documents. Decisions and rationale are captured and provide traceability.
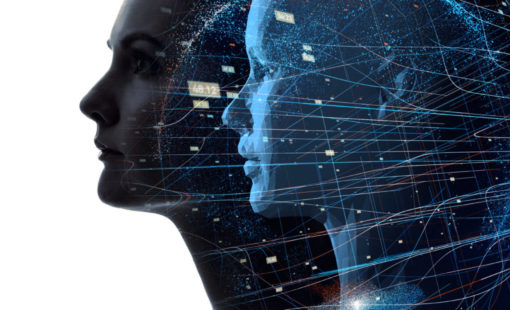
- White Paper
This eBook describes an MBSE based process for Electrical and Electronic design. The eBook begins with model content and structure with the purpose of implementation and the need for a “design envelope”.
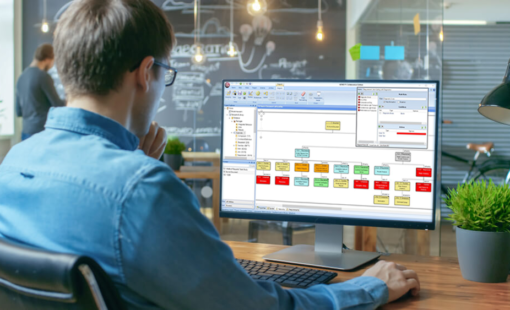
- Products
Digital Engineering requires a model-based design process that begins in Systems Engineering. Zuken acquired Vitech Corporation, a leader in Systems Engineering practices and MBSE solutions, with the intent of implementing an E/E model-based design process.
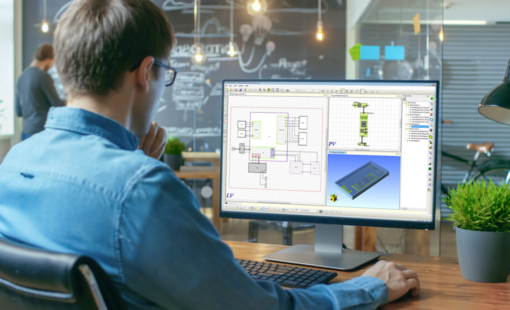
- Products
Digital Engineering requires a model-based design process that begins in Systems Engineering. Zuken acquired Vitech Corporation, a leader in Systems Engineering practices and MBSE solutions, with the intent of implementing an E/E model-based design process.