I hate to be the bearer of bad news and tell you that it’s going to happen again, but it’s going to happen again. There will be another major global event, a tsunami, an earthquake, a material shortage, or a global pandemic. Something that will make it very difficult to get your particular component, something that has the potential to make you go line down and suddenly you will be facing PCB component substitutions. It is going to be OK. There are always solutions. The options are out there; you just have to find them.
Component redundancy isn’t usually built into electronic designs; quite the opposite. Most things are optimized to within an inch of functionality. This is why a missing cap can shut down billion-dollar organizations. That’s OK; that’s just what natural competition hath wrought. Technology has also advanced to the point where there are many alternatives. But how do you know which ones will work? Which are effective alternatives? And, who are the reliable suppliers? First, we’ll identify some of the processes for making good PCB component substitutions. Then, we’ll look at a service like SE Connect from that can help us scour the nearly endless PCB component options out there.
SE Connect allows you to find which of your selected components are currently active and available. At the same time, you can identify the ones that have some supply chain risk. And it’s available right from within eCADSTAR, making it convenient and easy to use. The following guidelines serve as direction when making substitutions to mitigate the risk you’ll uncover with SE Connect in eCADSTAR.
Successful Passive PCB Component Substitutions
Caps, resistors, and inductors are often just after-thought components. That is until they cause a problem, until they fail, or are not available. Finding suitable substitutions can often be challenging. The standard order of operations in finding passive PCB component substitutions begins with finding matches in the mechanical aspects, then determining parametric replacements, and finally ensuring proper performance.
Mechanical
One of the critical aspects of finding suitable substitutions for passive PCB components is to ensure they match the mechanical aspects. This may sound obvious, but there is still some nuance to the process. First, consider tolerance. Most SMT components adhere to a standard size and shape set forth by organizations like the EIA. But sometimes, there isn’t a governing body to set standards. For example, through-hole components don’t typically have standards. Either way, it is good to review the tolerance. You want to make sure that even though the nominal size matches, the tolerance is still within the limits of what the PCB can accept. It is also possible to hack smaller components onto landing pads for bigger ones in a pinch, but that’s the last resort.
Parametric
Parametric matching refers to finding suitable PCB component substitutions with the correct nameplate values like resistance, voltage, capacitance, and current. Ideally, you want to find exact matches for all of these things. But when that’s not possible, some clever engineering can still get you what you need. For example, if you’re trying to replace a cap that goes on a 5V line, either 10V or 25V will do; you just need enough margin. More fundamental things like capacitance and inductance are usually limited to their prescribed values. I would be remiss in not mentioning tolerance; some applications can withstand going to a wider tolerance; that’s an engineering decision. That said, it is usually OK to move on to a tighter tolerance part.
Performance
This one is harder to judge and requires more than just looking at datasheets. Even after going through the exercise of matching mechanical and electrical characteristics, two components might have differing performance characteristics under operating conditions. For example, two parametrically identical ceramic capacitors might exhibit different capacitance vs. voltage or ESR vs. frequency characteristics. Your specific circuit requirements and design envelope will determine whether this is acceptable. Making such comparisons requires performing detailed simulations, often using vendor models or tools.
Successfully Subbing Active Components
Finding suitable PCB component substitutions for unavailable active components carries an extra level of complexity beyond just making sure that they are mechanically and pin-compatible. There are other factors such as power consumption and peripheral compatibility to consider.
Power Consumption
In many electronic systems, there is a constant battle against current demons that slowly draw extra power and drain your battery. It can take months to properly find and exorcise them to the proper current consumption level. If you happen to find yourself short an accelerometer and rejoice once you find a functional and mechanical replacement, make sure to remember to look at the current drain numbers in active and sleep mode as well as the quiescent current.
Peripheral Compatibility
Most of the features of our devices relate to function-specific components that enable a new capability, such as accelerometers, gyros, cameras, and other sensors. As you look to find second sources and substitutions for these components, keep in mind that they must be address-compatible. I2C interface devices don’t need to have the same device address; the software can handle that. However, you have to make sure that the devices don’t share the same address; you can’t have two devices on address 0x46. One final thing to consider is ensuring that devices with multi-function pins retain their options.
Checking the Health of Your BOM
Once your design is complete, it’s a good idea to check the health of your bill of materials (BOM) before submitting it. In the time it takes to finish a design, circumstances can change. You can check BOM health in eCADSTAR with SE Connect. SE Connect will provide an overall grade based on lifecycle, multi-sourcing, compliance, and inventory risk.
You can drill down to find the source of any risk to your design and filter by risk type to quickly identify various issues. The lifecycle will tell you whether a part is active or not recommended for a new design. SiliconExpert’s proprietary algorithm will forecast the number of years to end of life. In addition to reducing supply chain availability risk, SE Connect can also identify potential compliance gaps with regulations.
Using crosses can help mitigate risk. The software will identify any differences between cross-references to help with selection. Manufacturer names are presented so that you can choose from those that you have found to be reliable. Select a part number to see extensive parts. From there, you can view datasheets and product change notices. There is also a part search feature for those who wish to do their own research. Search by part number, manufacturer, and technology.
BOM risk can change with unexpected global events, and you can reassess periodically. We can’t predict what will happen next, but we can arm ourselves with the tools to react quickly. Natural disasters, factory fires, and geopolitical issues will disrupt the supply chain, but it doesn’t have to mean hours of research used for remediation.
De-Risk Your BOM Today
There are two ways to get started with SiliconExpert’s SE Connect. If you are an eCADSTAR user, it is easily accessible from the “Report” tab in the schematic editor. Once there, you can sign up for a 7-day free trial of SE Connect. Alternatively, you can access SE Connect directly from www.siliconexpert.com. Either way, knowing the health of your BOM and, more importantly, how to manage PCB component substitutions when you need them is a critically important skill for all engineers.
—
This post was co-authored by Dwight Morse, Senior Channel Marketing Manager with SiliconExpert
Dwight has spent his career in the software industry, moving from technical support to product management to marketing. He is passionate about integrating products in a way that benefits the end user, proving the whole is greater than the sum of its parts.
—
Related Products and Resources
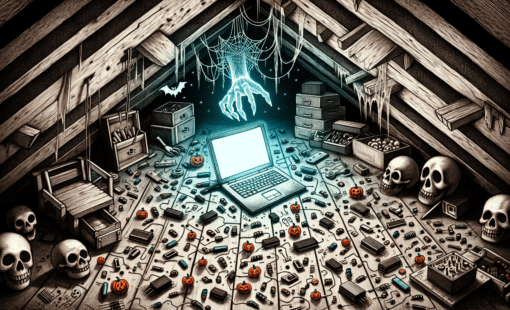
- Blog
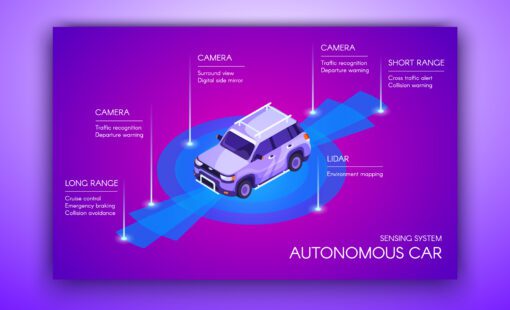
- Blog
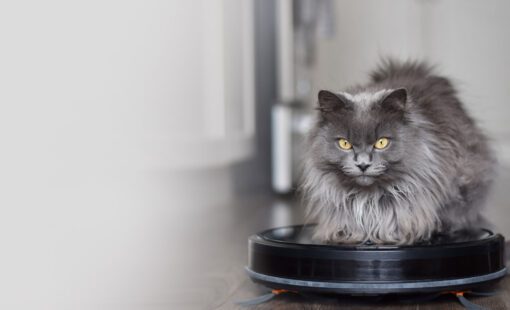
- Blog
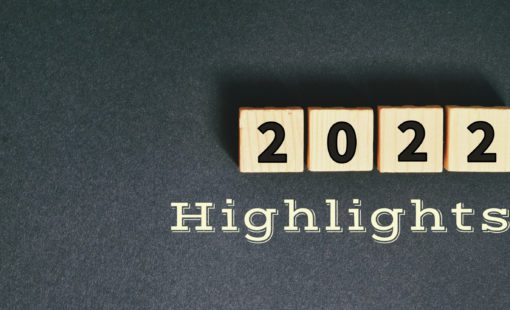
- Blog