If you don’t work in the marine industry, you might not be aware of the extent of technical advancements that have been taking place in the sector over recent years. This has resulted in a massive increase in project complexity which has created many challenges for the people in charge of electrical system integration.
Traditional methods are really struggling with these demands – you’d have to be Einstein to deal with this complexity using only pen and paper. The upshot is that engineers (if they haven’t already done so), are being forced to rethink their design processes and environments. They can no longer rely on pen and paper, or a generic CAD system for creating the complex electrical systems in today’s marine applications.
But no need to jump ship, electrical design software that may have more traditionally excelled in machinery and automotive applications can also be used in marine projects too – yes I’m talking about E³.series.
Background – The sources of the complexity
The extensive use of automated computer control systems for machinery controls, navigation, radars and passenger/crew safety systems, along with the return to electric propulsion systems, are the source of this complexity and call for fully integration management onboard.
The majority of all vessels now need some form of electrical integration, which is magnified as the size and complexity of the vessel increases. In addition, equipment is likely to be sourced from multiple suppliers often working to different standards that need to communicate— and be connected together—all this involves complex cabling networks and panel design.
The increase in electrical power required to feed all these applications has also spurred a rise in higher voltages being transported around the vessel, so cabling needs to perform to the highest of safety standards.
If that wasn’t enough, these compatibility, consistency and new technology challenges have driven the rise in international standards, which require full traceability and documentation of electrical systems too.
Overcoming the electrical issues
There are some common issues faced when designing electrical cabling networks onboard, such as
- Defining the required gauge of a cable (the external diameter of the cable related to the copper conductor width) and accurate lengths of cable – choosing cables
- Dealing with changing requirements
- Safety issues associated with possible electromagnetic interference that could result in unintentional signals being transmitted or commands being performed. Imagine a short circuit on a warship ‘accidently’ firing a missile? That sounds a bit extreme and granted, yes it is, but it explains the importance of my point well I think.
And guess what? Yes, E³.series can be integrated within the design process to overcome these electrical system integration problems.
Example 1 – choosing cables
Let’s take E³.cable, which helps engineers create block diagrams and schematics.
The type of cable used in different environments and situations can also be simply managed within E³.cable. In an engine bay for example, cables that can withstand higher temperatures are essential. When choosing a cable within E³.series, you can specify the name, diameter and gauge, or pick from a predefined drop down list of industry-standard cables.
Example 2 – dealing with changing requirements
The introduction of a new satellite navigation system two years into the design of a large complex vessel would normally result in extensive rework of the electrical cable design, but with E³.cable it is as simple as updating a single sheet; other areas within the electrical system will automatically be modified to reflect the changes.
Final note
The most significant benefits, of using software like E³.series aside from the day to day design layout, verification and 3D viewing capabilities; is their flexibility and ability to deal with changing technology and functionality to generate all the required purchasing and manufacturing data while integrating with other design systems.
- For more information you can visit Zuken’s marine industry web page.
There are many other ways to simplify electrical system integration within marine projects, maybe you have experience of them and would be willing to share your experiences in a comment below?
Perhaps you work in another industry and want to comment generally on simplifying electrical system integration, any comments welcome…
Related Products and Resources
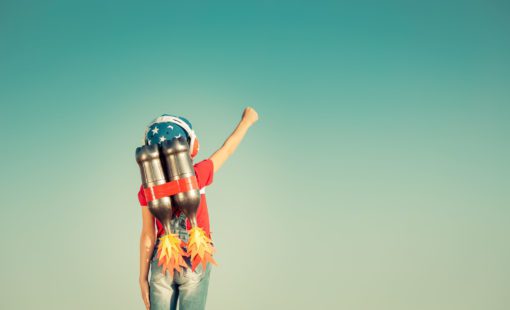
- Test Drive
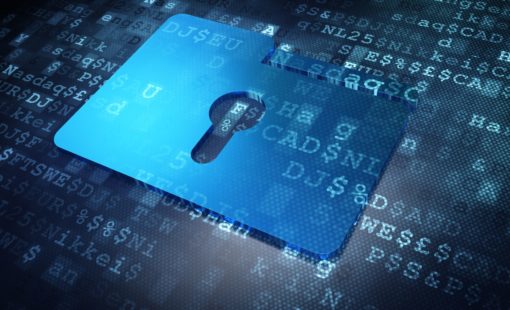
- Products
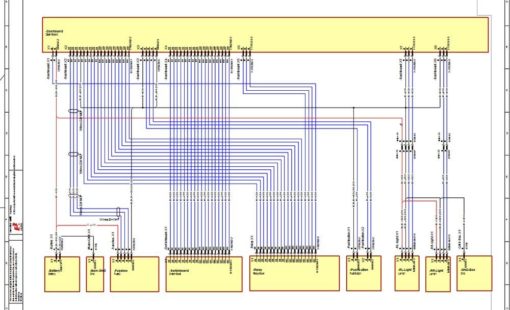
- Products
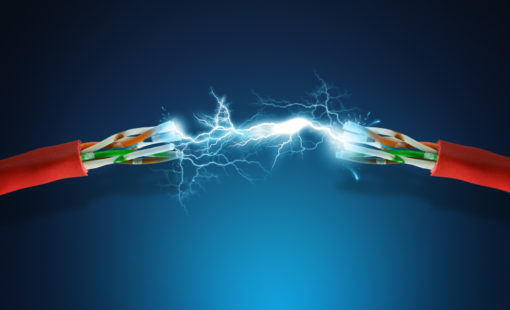
- Products
E3.series is a Windows-based, scalable, easy-to-learn system for the design of wiring and control systems, hydraulics and pneumatics. The out-of-the-box solution includesĀ schematic (for circuit and fluid diagrams),Ā cable (for advanced electrical and fluid design),Ā panel (for cabinet and panel layout), andĀ formboard (for 1:1 wiring harness manufacturing drawings). Integrated with MCAD, E3.series is a complete design engineering solution from concept through physical realization and manufacturing output.