The Growing Importance of Cost Efficiency in Wire Harness Production
In today’s world, wire harness manufacturing cost reduction is no longer optional; it is a survival strategy. With increasing product complexity, volatile supply chains, and rising labor and material costs, manufacturers face mounting pressure to deliver faster without compromising quality. As electrification expands across industries, wire harnesses are becoming more intricate, yet customers continue to expect faster delivery and top-tier quality.
That means cutting corners is out of the question. The challenge lies in optimizing design and production for manufacturability while maintaining product integrity. Fortunately, modern design tools and streamlined processes are helping manufacturers do just that.
1.Design for Manufacturability (DFM)
Wire harness cost optimization starts with smart design. When harness designs are overly complex or fail to account for how they will be built, they often lead to delays, rework, and added costs. This is where Design for Manufacturability (DFM) plays a crucial role. Designing with the production floor in mind helps reduce assembly challenges, shorten build times, and improve consistency.
For example, breaking larger harnesses into smaller, more manageable subassemblies enables parallel assembly on smaller workstations. Another consideration is allowing extra slack in tight spaces where the bend radius is under pressure, which makes installation easier. Small adjustments at the design level can significantly reduce manufacturing friction.
Tools like E3.series support this process by integrating mechanical constraints directly into the electrical design using E3.3DRoutingBridge. With just a few clicks, teams can align electrical schematics with mechanical realities. This collaboration eliminates guesswork and minimizes trial-and-error, resulting in shortened development cycles, and harness designs that are accurate and on-schedule.

2.Manage Revisions Effectively
Design changes are inevitable, but poor revision management can introduce significant costs late in the development cycle. A missed pinout change, for example, can lead to failures during hardware-in-the-loop (HIL) testing or assembly, causing delays and unplanned rework.
This is where revision control becomes essential and why tools like DS-E3 are so valuable. They allow engineering and manufacturing teams to manage revisions and analyze impacts collaboratively in real-time, helping identify potential costly mistakes before they reach the production floor. Coordinated collaboration builds trust between engineering and manufacturing, improving quality while supporting overall wire harness manufacturing cost reduction.
3.High Speed Production with Digital Work Instructions
Traditional paper-based instructions are outdated. They are difficult to manage, slow to update, and prone to misinterpretation. They also place a high burden on experienced assemblers who may rely on tribal knowledge to fill in the gaps.
Digital work instructions address these issues by providing real-time, visual guidance specific to each harness. Interactive displays improve clarity and reduce mistakes on the assembly floor. These tools also accelerate the training of new workers, offering greater flexibility throughout production.
Save Smarter, Not Slower
Wire Harness Manufacturing cost reduction does not mean sacrificing quality. With the right tools and strategies—like DFM, effective revision control, and digital work instructions—teams can cut waste, streamline production, and build better products. It all starts with a smart design approach. Investing in platforms like E3.series and DS-E3 empowers your team to work more efficiently and collaboratively across disciplines. The result is a more reliable, cost-effective process from design through delivery.
Ready to take your harness manufacturing to the next level?
Explore Zuken’s wire harness design tools and discover how to reduce costs without compromising quality.
Related Products and Resources
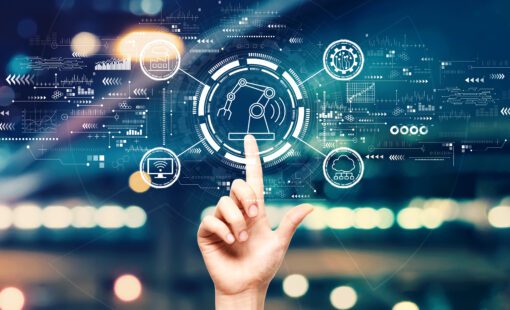
- Webinar
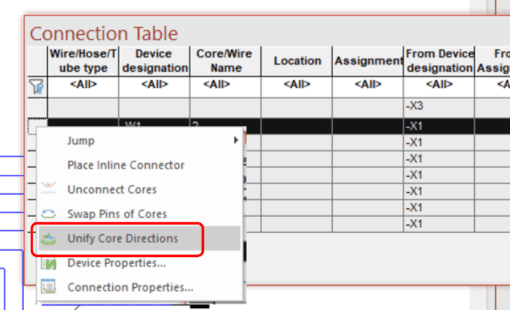
- Press Release

- Pages
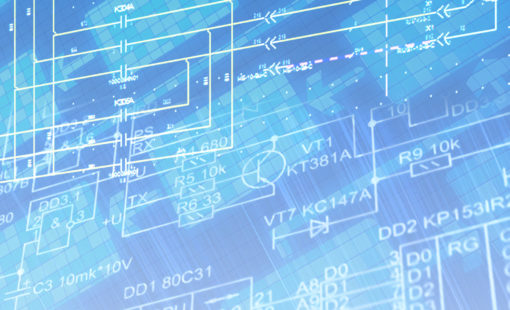
- Brochure