After having looked at how electrical engineers can impact the product development process by working with sales and systems engineering in the last two posts in this series, now I’m going to move onto testing and manufacturing.
Testing
You might be lucky enough to be in a large organisation that has a dedicated test department, whose function it is to provide test solutions to all products. This makes the problem of testing a little easier because liaison with this department can greatly reduce any risk involved in testing any product, complex or not.
You can make both of your lives easier if you get together to talk about thermal considerations, short circuit tests, continuity, load, EMC / EMS and signal integrity tests etc.
If you are not one of the more fortunate ones and you don’t have a dedicated department for this then you’re going to have to take care of these things yourselves.
If Automatic Test Equipment (ATE) is being used, then you should be thinking about the way this equipment is connected to the design. In the case of an electrical harness, a test harness connector could be required to facilitate testing when the product has been fitted and assembled in the project, also this would enable the re-testing of the product during any routine maintenance.
Manufacturing
It can’t get much more fundamental than making sure the designs are manufacturable.
This is not just about thinking ‘can this be made or constructed’, but you need to consider the economics and physical constraints of the process…
a) How easy is the assembly or disassembly of the product?
b) Is there easy access to internal components or connections?
In order to design for manufacturability, everyone in the project team needs to understand how products are manufactured through rules and guidelines. With manufacturing participation, you as the electrical engineer can get the design made, and participate in the design of the processes to be used to build the product they are designing. Working with manufacturing can deliver designs that are simple and inexpensive to make, that are also easy and inexpensive to service and support.
Another benefit is that costs and time-to-market are often cut in half, since products can be quickly assembled from fewer parts. Making the products easier to build and assemble, in less time, with better quality. And there, you have got yourself some more new friends, in manufacturing – who are appreciating your work.
photo credit: Niffty..
The very act of working closely with manufacturing encourages design re-use, standardisation of parts, maximum use of purchased parts, modular designs, and standard design features. All this ends with significant improvements in quality and delivery, with a higher ratio of happy customers! What more can the directors want???? Forget I asked that question…the list will be endless.
Next time I’m going to look at how you can make an impact by working with mechanical designers.
Talk to you next week.
p.s I recently did a webinar on electrical testing in the aerospace industry, click here to find out more.
Related Products and Resources
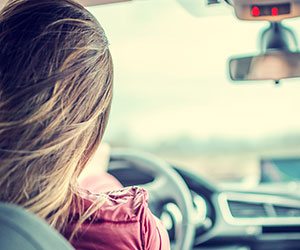
- Test Drive
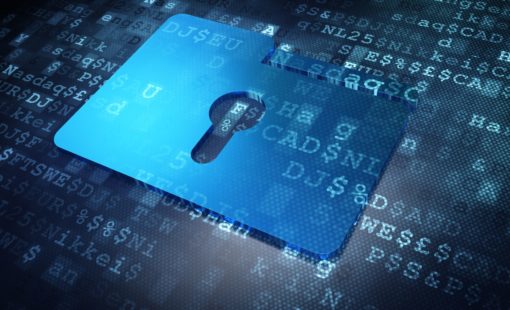
- Products
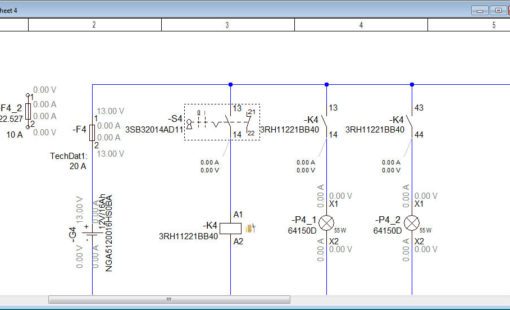
- Products
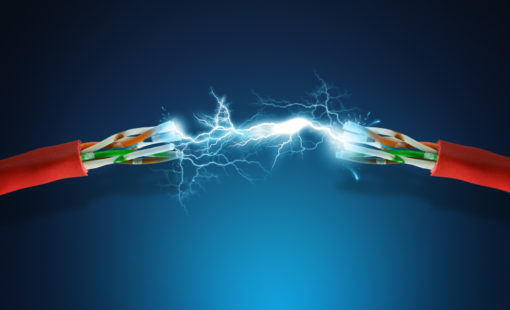
- Products
E3.series is a Windows-based, scalable, easy-to-learn system for the design of wiring and control systems, hydraulics and pneumatics. The out-of-the-box solution includes schematic (for circuit and fluid diagrams), cable (for advanced electrical and fluid design), panel (for cabinet and panel layout), and formboard (for 1:1 wiring harness manufacturing drawings). Integrated with MCAD, E3.series is a complete design engineering solution from concept through physical realization and manufacturing output.