The Digital Transformation and, in turn, Digital Engineering continues to be a focal point at Zuken. More and more companies are turning to digital processes for their complex product designs. Therefore, we’re developing digital solutions to replace outdated, error-prone document-based processes. System-level modeling, also known as the Digital Twin, plays a significant role in digital engineering. The digital twin replaces the traditional design-build-test methodology by providing the basis for a more modern model-analyze-build process.
Building Digital Engineering Processes
As Zuken works to build these digital processes, partners play a significant role. This post announces our newest digital engineering partner, Electro Magnetics Applications (EMA). EMA excels at modeling coupling to cabling and systems for lightning, high-intensity radiated fields (HIRF), electromagnetic compatibility (EMC), and space plasma environments. EMA also helps commercial and military customers identify and mitigate complex RF interference problems for space, ground, air, and sea platforms.
Founded in 1977, EMA has a long history that includes the analysis, hardening, and testing of systems such as the Space Shuttle, military and civilian aircraft, various missiles (e.g., Minuteman, Peacekeeper, Trident, Pershing, and many smaller systems), ships, and tanks.
Model, Analyze and Build
EMA develops a tool known as EMA3D. The software runs simulations addressing HIRF and lightning requirements early in the program before physical prototypes are complete. The key phrase here is “before physical prototypes are complete.” This early analysis approach is necessary for today’s complex aircraft, vehicle, and systems designs. As part of the digital engineering philosophy, it is essential to identify design errors before physical prototyping. Errors found during the physical prototyping stage are costly and could be irreparable. Complex products and systems, which most are these days, require this model-analyze-build digital engineering process.
So why EMA and EMA3D? A couple of reasons. First, Zuken is heavily vested in wire harness and cable design solutions with our E3.series product. And secondly, Zuken is actively building out digital engineering processes that support the model-analyze-build approach. When you combine these positions, you get EMA and EMA3D. E3.series is an industry-leading solution for wire harness and cable design used by companies worldwide and across all industries. It is versatile, reliable, and scalable for the enterprise user. However, to support Zuken’s digital engineering initiative, we needed a system-level analysis capability for EMC and HIRF. EMA checks all the boxes.
Wire Harness Design with EMA 3D
Let’s take a minute and quickly review the digital engineering process for wire harness design. We’ll start with a SysML model constructed in GENESYS. GENESYS is a model-based systems engineering (MBSE) design environment; part of Zuken’s recent Vitech Corporation acquisition.
Digital engineering implies a design process based on MBSE. Once we have a model developed in GENESYS, the electrical portion of the model moves into E3.series for implementation. The result is the transfer of the logical architecture to E3.topology. The MBSE model is connected to the detailed design process and provides a design envelope to the design team. From that point, the engineering department can view diagrams, requirements, and parameters without ever needing to launch GENESYS or learn the MBSE tool. Now that the detailed design is complete, we are ready to move into the analysis phase. In the near future, Zuken will release an automated process to replace to move model data between tools, replacing the current error-prone manual process. Keep an eye out for upcoming announcements.
EMA3D Completes the Story
Using E3.series to design the electrical portion of the model, engineers will export a KBL file and import it into EMA3D. Once in EMA3D, detailed design information regarding the harness geometry can be added to EMA3D’s system-level model in preparation for analysis. Then, EMA3D will perform a range of simulations looking at the radiated coupling to cables, radiated emissions from cable, coupling through shields, EMU crosstalk between cables, and much more. If you are using E3.series for wire harness design and are looking for a way to analyze the cable network within a complex platform, then EMA3D needs to be on your shortlist.
Related Products and Resources
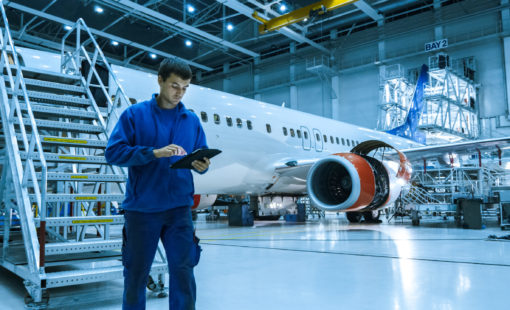
- Products
The Digital Thread is a foundational element of a successful Digital Engineering implementation. Digital conversations involving procurement, design, manufacturing and field service replace email and paper documents. Decisions and rationale are captured and provide traceability.
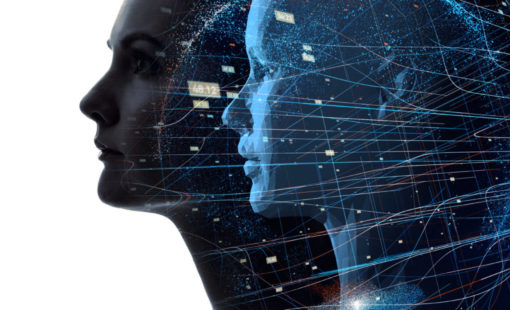
- White Paper
This eBook describes an MBSE based process for Electrical and Electronic design. The eBook begins with model content and structure with the purpose of implementation and the need for a “design envelope”.
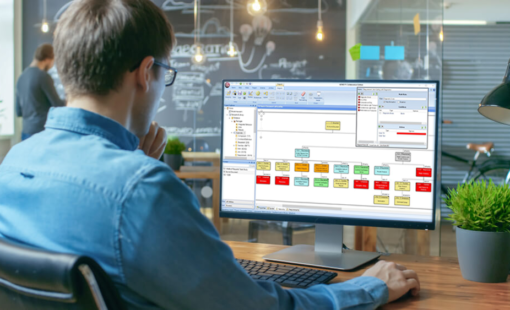
- Products
Digital Engineering requires a model-based design process that begins in Systems Engineering. Zuken acquired Vitech Corporation, a leader in Systems Engineering practices and MBSE solutions, with the intent of implementing an E/E model-based design process.
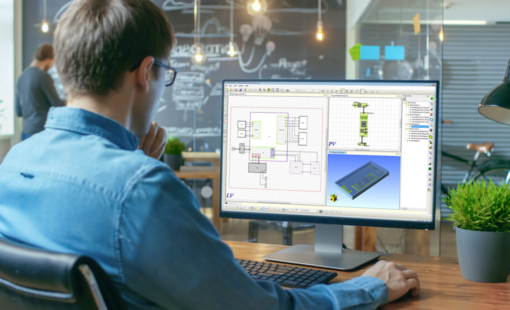
- Products
Digital Engineering requires a model-based design process that begins in Systems Engineering. Zuken acquired Vitech Corporation, a leader in Systems Engineering practices and MBSE solutions, with the intent of implementing an E/E model-based design process.