A 3D design process has many advantages over a 2D design process. The number and effectiveness of these advantages varies with the complexity of the system. A well-managed 3D cabinet design process can reduce time and error by more than 50%. Consider the mechanical design space; an overwhelming majority of designs use 3D solid modeling applications. However, the electrical design industry cannot say the same. The key to accelerating a 3D design process is to use a design solution capable of bridging the gap between 2D and 3D design methodologies.
Manufacturing Supply Chain and Design Challenges
Having experienced the results of a weak local supply chain, shoring up local manufacturing is fast becoming the top goal for many governments and industry leaders. Today, low capacity and high demand are the top challenges for the manufacturing sector. Often even small flaws in any process are exposed when subjected to high pressure. The unprecedented demand cycle is reducing timelines and increasing delivery pressures, further exasperating an already stressed system.
Control cabinets are commonly found in various applications like power distribution, controls, automation, large machinery, factories, and many more. Interestingly, there are some common challenges across these industries.
The challenges often at the top of the list are:
- The predominantly two-dimensional design process.
- The lack of manufacturing information in the design process.
- Little to no design-for-manufacturing solutions.
- Outdated manual processes for electrical design.
- Minimal and complex instruction sets from engineering to manufacturing.
A robust 3D design process using the right parametric design tool provides the best solution to these challenges. Consequently, to meet these challenges head-on, many companies are adopting E3.series tools.
3D Cabinet Design Challenges
Designing in 3D opens the possibilities to do many quality checks and use design-for-manufacturing techniques unavailable on a 2D platform. Which is to say, it is easy to check for collisions between two devices while placing them and to ensure the door will close without interference. Additionally, a 3D design environment makes it easier to plan for often overlooked wiring and other assembly activities. Furthermore, an intelligent 3D design environment can drive an automated cabinet cutting, milling, and assembly process. Most importantly, the designs built in a 3D platform perform better with fewer iterations on the manufacturing floor.
So, why is the electrical industry moving so slowly toward adopting 3D cabinet design? The slow rate of adoption is largely due to the most common challenges with a 3D design process: steep learning curves and increased complexity. Firstly, in the electrical design space, the schematic and the rest of the design is 2-dimensional. Secondly, 3D inherently adds a new dimension of complexity and requires a change in perspective. Thirdly, it often requires expertise in manipulating complex spatial elements. As a result, many electrical teams consider the adoption of 3D as an unacceptable overhead.
Nevertheless, there are many good reasons to find ways to mitigate the challenges of 3D cabinet design. For instance, a design platform like E3.series creates possibilities by driving the 3D design through a 2D user experience. More precisely, a user designs the cabinet in the 2D view, and the 3D view is automatically updated.
Cabinet Design in E3.series
E3.series parametrically connects a physical cabinet and the logical schematic. In addition, with the help of the intelligent design library, it simultaneously represents the cabinet in both 2D and 3D. The design teams have many options to define their desired processes. The design can start from the cabinet, the schematic, or even the bill of materials.
The option of physical representations in both 2D and 3D greatly enhances the assembly process. The library maintains the allocation of mounting requirements, cut-out details, and space requirements, reducing mounting and spacing inconsistencies while enabling automated drilling and milling options. Furthermore, the wiring process considers the physical wiring limits of each pin on a component. Ducts define the path for wires, and their size determines the number of wires to route through them.
Zuken is working with key industry partners to explore the future of automated cabinet building. Learn more here.
2D Designs for 3D Outcomes
In E3.series, the 2D views simplify the cabinet design process. Specifically, the 2D views in E3.series are flattened views of the 3D design space. The act of placing components in the 2D view triggers a variety of automated actions. Firstly, E3.series DRCs check for mounting compatibility of the devices. Secondly, the active collision checks take a 360-degree view of the placement area to avoid collisions. Thirdly, the system considers the 3D orientation of the object before completing the placement.
The simplification of component placement in a complex environment significantly improves the design accuracy and space utilization. Moreover, the option to see the schematic logic of the devices place in the cabinet helps the designer select the optimum placement location. Furthermore, the automatic wiring options complete the routing of the panel wires driven by the logical connection in the schematic, space constraints, and configurable routing rules.
2D and 3D Cabinet Design Process Considerations
Although the precise design process varies from team to team, there are some fundamental process options to consider to take advantage of the 2D and 3D design options in E3.series:
- Start with capturing assembly information
- Capture simple dimensions to manage space for components.
- Add STEP files for 3D visualization and detailed views.
- Capture all mounting options for the component.
- Add wiring details
- Establish internal min and max wire sizes for a component pin.
- Confirm the maximum number of wires for a component pin.
- Optionally, capture the end treatments to be used for a connection.
- Define the standard flattening options for a 3D cabinet
- Consider standardization of a cabinet to flatten like a book, or a shipping box, or some custom pattern.
- Capture component mounting surface like inside, outside, or both.
- Establish standard cabinet types and sizes, if possible.
- Create standardized panel assembly rules
- Create standard rules for mounting and spacing requirements.
- Establish standardized keep-out zones for holes and cut-outs.
- Consider space for tools and wire bends in space requirements.
- Drive automated manufacturing options
- Capture information for driving automated cutting and milling machines.
- Confirm label and tagging formats conform to automated labeling machine options.
- Consider wiring automation options driven from the design.
Read more about automated manufacturing options with E3.series:
READ MOREConclusion
In summary, the electrical automation and manufacturing sector needs to improve throughput without sacrificing quality or profit margins. Adopting a robust 3D electrical design process is a key step towards reaching that goal. Although the industry has been slowly moving towards adopting 3D cabinet design, an effective resolution requires a quick, seamless transition.
Zuken’s E3.series design suite provides a robust parametric electrical design tool with simplified 2D to 3D cabinet design options. Most importantly, creating connected views, capturing the manufacturing and wiring details, and the fundamentally connected design platform together make E3.series the most effective 3D cabinet design solution.
Related Products & Resources
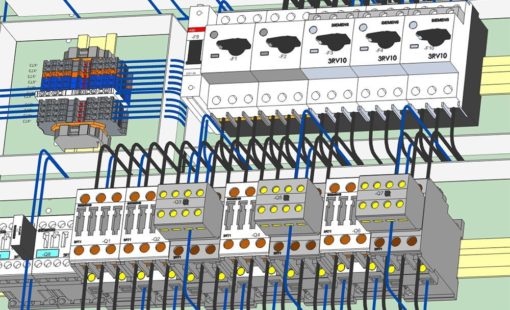
- Products
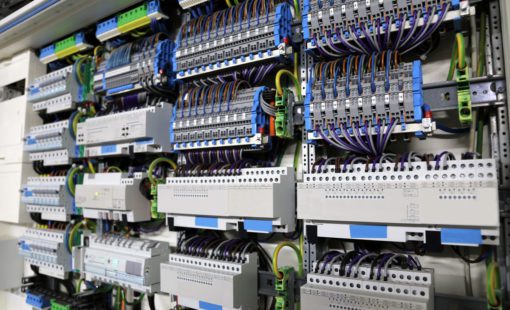
- Products
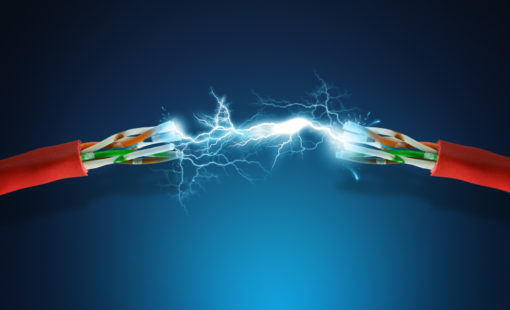
- Products
E3.series is a Windows-based, scalable, easy-to-learn system for the design of wiring and control systems, hydraulics and pneumatics. The out-of-the-box solution includes schematic (for circuit and fluid diagrams), cable (for advanced electrical and fluid design), panel (for cabinet and panel layout), and formboard (for 1:1 wiring harness manufacturing drawings). Integrated with MCAD, E3.series is a complete design engineering solution from concept through physical realization and manufacturing output.